Rising damp
Following on from the revision of Clause E2 (External Moisture) of the Building Code in 2011, Progressive Building talks to Brian Greenall of the Waterproof Membrane Association to see how its own Code of Practice is progressing.
Progressive Building: The Waterproof Membrane Association Incorporated (WMAI) has been working on a Code of Practice covering below-grade waterproofing following the omission of any standards in the revised Building Code. How long will it be before you have a draft ready for consultation?
Brian Greenall: We’re expecting the process to take another nine to ten months. Basically, once we have what we consider to be an appropriate draft then the next step – which is the same process we follow with all our codes regardless of their ultimate destination – will be to send it out for public comment. At that point, interested parties – applicators, specifiers, local authorities, MBIE themselves – can read the document and comment on the document.
Then we do a review process where we take all the comments and go through and determine whether they’re persuasive or non-persuasive, or whether we should adjust anything and then we come up with a final draft copy, which then goes through the process of final checking and finally becomes the document, so it is quite an involved process and requires a great deal of work on our part.
PB: Has this actually been a blessing in disguise? Have you been able now to address areas that perhaps weren’t covered in the initial regulations?
BG: Short answer, no. The original E2/AS1 statement was relatively all embracing, albeit fairly loose in its administration. What you need to understand is that there’s a lot of difference between something written in the E2/AS1 and the Code of Practice we’re developing. The code covers a lot more items as well as detailing, material choice, application processes and conditions. All of those sorts of aspects go into one of our codes of practice.
So the two or three paragraphs that were in E2/AS1 end up being a 60 to 80-page document. That said, it’s not a statement of what this [particular product] should or shouldn’t do; it’s a total statement of what is available to the industry, which type is best suited to a particular purpose, how you detail them, how you ensure that what you put in the ground will actually perform. Which is the whole intention and is what we’ve already done with the Torch-on Roof Membrane and Wet Area Membrane codes.
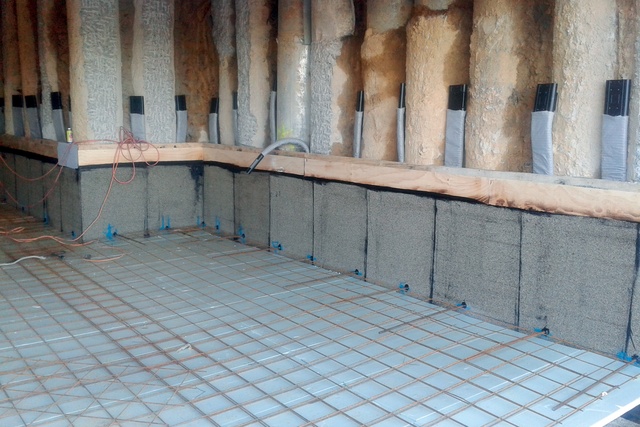
PB: One of the concerns raised by the exclusion from the code is that there is no regulation of who can and can’t claim to be a waterproofer…
BG: Exactly right. The problem we have at the moment is that the way the LBP system works is that all manner of non-specialists can waterproof different things. For example, a plumber is, as I understand it, a qualified waterproofer because he does penetrations through a wall, which is a bit bizarre. Similarly, a roofing LBP is in theory, although not in practice, qualified to basically do any form of membrane roofing at all, because he can sign it off.
So what we’re trying to do is remove these sorts of anomalies and put the use of a waterproofing system under one umbrella, if you like, and that’s the umbrella we’re working on. Our ultimate aim, as a waterproofing industry, is to have waterproofing recognised as a legitimate building trade and therefore, being subject to the same regulations as other LBPs. It seems sort of idiosyncratic that anybody can stick anything on the below-grade areas of a building and not be subject to any form of stipulation as to their ability to perform or the ability of the product they’re using to perform.
At the moment the system is dependent on a lot of whims and particularly a lot of whims in terms of the Building Consent Authorities (BCAs), because they don’t necessarily know which is best. So it becomes very much a reliance upon dealing with a reputable supplier and a reputable applicator in the first instance. Our aim with this code is to create a standard for the whole construction industry, not just the waterproofers themselves but for all the components of it – main contractors, specifiers, BCAs, everybody.
PB: What about the products themselves? Is that an area of concern in terms of substandard products?
BG: The problem with below-grade waterproofing is that there are a number of ways of dealing with the issue and an equal number of products in the marketplace that fail to adequately do so. So what we’re trying to do is ensure that the materials perform to a standard and to educate people as to the choice of product. Ultimately, however, it behoves the specifier to determine if someone is offering a legitimate product for their specific needs.
PB: Can we not legislate against that to essentially remove ‘shonky’ products from the market?
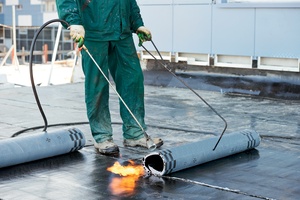
BG: That’s one of the difficult things in this particular instance. With Torch-on Roof Membranes we were able to qualify them with some fairly simple tests, which could be used to validate the quality of the product and its performance when laid. With the Wet Area Membranes it was a little bit more difficult but then we utilised the basic methods from AS4858 and worked from that.
So, once again people were give a choice of product and given a scenario as to when a certain type of product would perform better than another product. That’s more or less what we’ll have to do in this case, because it gets wider as we’re dealing with various types of products. That scope then means the qualification of the product and determination as to whether it will perform or not becomes quite difficult for us to do.
PB: In terms of this process, of getting this all put to rest has that made you consider that the rest of the regulations need to be looked at?
BG: We don’t really do that, what we’re doing is responding to consumer demand, the consumer being the construction industry, but also we’re desirous of ensuring that any area in which a waterproof membrane is used is covered by a code of practice, which then gives a better assurance to everybody that what they do will actually work properly. We still have not yet addressed external liquid membranes; we still haven’t addressed other types of roofing membranes other than torch-on membranes.
So there’s a programme going forward that we’ll gradually roll through. But the order in which we do them does depend to some extent on demand. In this case we were going to do external liquids as a logical follow on from internal wet area membranes. We didn’t because this situation then arose where there was nothing determining what was a satisfactory tanking membrane and how you actually went about tanking a building.
PB: So what, ultimately, from your point of view, is your goal?
BG: Unfortunately, the structure doesn’t allow for more LBPs at the moment. Logically, there needs to be something akin to an LBP for waterproofing so that people are assured that the person who is doing and/or signing off waterproofing work is qualified to do so, giving both the client and the BCA peace of mind that the work has been done properly and with the right materials. That’s the long-term goal; right now under the current framework we can’t achieve that goal.