Raising the frame
Progressive Building magazine talks to Kiwi entrepreneur John Oliver, whose stunningly simple Codemark-certified system looks set to change the way we build.
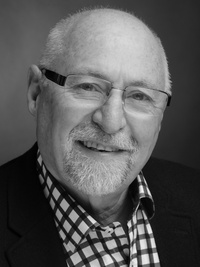
Progressive Building: What is the Hiandri system?
John Oliver: The Hiandri system was developed specifically as a response to the leaky home syndrome.
It involves the placing of plastic packers under the bottom plate at 600mm crs, lifting the entire timber frame 12mm above the floor. This allows water to escape and stops the timber from acting like a blotter, soaking up water through the frame.
Because moisture is free to escape, the system removes the need for a damp proof course.
PB: Why does the system work?
JO: The more I thought about this system, the more advantages the plastic packer concept revealed.
With the system, should water enter the building at any stage in its life, develop a leak for whatever reason, or have a leaking pipe, the moisture from that leak is managed.
Any water running down the frame on reaching the underside of the bottom plate, will drip onto the floor and run outside the building, mitigating any issues.
Even if water was to go inside the building, a wet patch would appear immediately alerting the tenant to an issue, meaning that leaks are found quickly before they cause expensive or major damage.
PB: How is this different to how we have been building until now?
JO: The way we have been building in New Zealand to date means when water runs down the framing, it hits the bottom plate, tracks under it and is held in this position for an invariably long period of time. The moisture builds up, continually being added to, and creeps several metres both ways along the bottom plate undetected, rising up through the studs and framing and resulting in major rotting of the framing and surrounding timber.
PB: Does it have any other benefits?
JO: The system also reduces building costs by allowing builders and owners to ensure the early construction phase can move along swiftly, as opposed to waiting weeks for the house frames to dry prior to installing the wall linings.
In New Zealand, framing timbers should not exceed 20 per cent moisture content prior to being lined. In our often-wet climatic conditions, this can mean waiting weeks for frames to dry. A bottom plate high in moisture content effectively acts as a barrier, preventing moisture from dissipating freely. With the raised bottom plate, this problem no longer exists as water is free to dissipate through the gap between the bottom plate and floor.
PB: Is the system certified as an acceptable solution?
JO: Yes, to launch the system nationwide we needed product certification. In May 2014 we obtained CodeMark certification, which in effect means all territorial authorities have to accept the system as an acceptable solution.
PB: What bracing systems are the packers approved with?
JO: The system is currently approved for use with four bracing systems.
PB: What are the packers made out of?
JO: They are made out of tough, durable polypropylene plastic that cannot absorb moisture and transfer it to the timber or on to metal framing.
PB: Is this a solution for both residential and commercial applications?
JO: Yes, the packers can be used in a variety of buildings, but must be installed in accordance with the current installation manual.
PB: How did you come up with the idea for the system?
JO: In the last 20 years the building industry in New Zealand has gone through turmoil. The words ‘weathertightness’ and ‘leaky home’ have been central to this turmoil. As a concerned Kiwi, I thought there had to be a simple solution that would go a long way towards helping the problem, and in 2004 I came up with the idea of placing plastic packers under the bottom plate.
I knew from experience as a brick consultant how robust the cavity is for brick veneer, and applying these same principles to the timber bottom plate of framing just made sense. After bouncing the idea off several people in the building industry, I promptly took out a patent not only on the packer, but also on the methodology of raising the bottom plate.
PB: What do you see as the future for Hiandri?
JO: The immediate benefits of the system are obvious, but the real future for this system as I see it are the long-term benefits it offers all New Zealanders. It virtually eliminates the possiblity of timber frames rotting due to moisture ingress. It works because it is simple. I firmly believe that within five to 10 years the vast majority of frames manufactured in this country will be installed using this system.
PB: How has it been received in the market so far?
JO: The system has been available for about six weeks. In that time, around 100,000 units have been sold, which has endorsed the need for this sort of system and solution.