Prefabrication: Better, cheaper, faster
Chris Barton talks to three firms deeply committed to offsite manufacturing. Will this give new meaning to the role of the architect as master builder?
Many believe increased use of offsite manufacturing will work wonders for solving our housing crisis – not just in breaking the duopoly stranglehold on the cost of materials but also by transforming the way we build, resulting in dramatically shortened building times and more housing. Others are sceptical, pointing out almost all traditionally built housing has some level of prefabrication – usually the small components of frames, trusses, joinery and cabinetry - which accounts for a third of the cost of building.
Chief executive of the New Zealand Building Industry Federation Bruce Kohn is one such sceptic, writing in the New Zealand Herald recently that “complete offsite construction of housing is generally no cheaper than traditional on site home building”.
Offsite manufacturing advocacy group PrefabNZ begs to differ: “Prefab delivery can mean a saving of about 15 per cent in total construction cost – $32,000 for a 157m2 house.” Plus huge savings on time to build – 60 per cent of construction time can be reduced through offsite construction.
Some among PrefabNZ’s membership imagine, with a little help from government – if it ever gets its KiwiBuild scheme back on track – a future of five to ten companies producing 500–1000 houses a year in large, offsite factories, whether by flat pack panels, volumetric components or a mix of the two.
Are they dreaming? What would such a change mean for architectural practice?
You always want to duplicate
Daiman Otto has some telling statistics: “Something like 80 per cent of the people didn’t care about how the building was built; 10 per cent were interested in how it was built; and 10 per cent bought because of the way it was built”. Tallwood’s director of design and digital construction is talking about Forté Living, a 10-storey, prefabricated apartment tower built in Melbourne in 2014 from Austria-sourced cross-laminated timber (CLT).
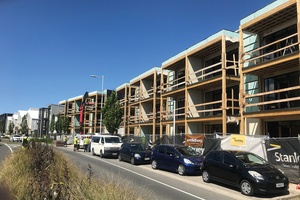
Otto reckons it would be a similar story for The Grounds, a prefabricated, three-storey walk-up comprising 44 apartments at Auckland’s Hobsonville Point. It, too, is made of manufactured timber: a jigsaw of CLT floors and ceilings; internal laminated veneer lumber (LVL) posts and beams; and treated exterior glulam post and beams for the balconies, breezeways and external stairs.
The ambivalence about prefabrication – “prefab is not a dirty word” as Pamela Bell, founder of advocacy group PrefabNZ, is fond of saying – is reflected in The Grounds’ marketing. It’s only peripherally about offsite manufacturing: “Designed using low-embodied, naturally renewable timber material, this boutique apartment offering will be built within 10 months with a smaller carbon footprint thanks to the use of natural materials and off-site prefabrication”.
Even if most people couldn’t give a fig about how the building is made, The Grounds is a showcase for transformational offsite manufacturing. “This is a pilot project, not a prototype, because it’s using tested systems,” says Otto, choosing his words carefully. “We wanted to prove that you could build a three-level building using offsite manufacturing and make it as affordable as conventional building but quicker.”
On site in late January, he’s quick to admit the build, which began in January 2018, has missed its December completion date. There have been glitches: “Weather. Concrete slabs. Coordination. That kind of thing,” he says wistfully. “It’s still quick compared with a conventional building just not as quick as we envisioned.”
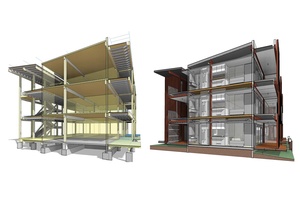
But the real benefit of the Hobsonville Point showcase is already under way. The same three-level walk-up typology is being repeated in a rental complex of 66 apartments for Housing New Zealand on the corner of Cessna Place and Bader Drive, Mangere. This time, the schedule is on track. Building started in October last year and will be finished by the end of June. That’s a lot of housing in just nine months and the sort of project that, if enough companies were doing the same, could go a long way towards making KiwiBuild’s abandoned annual building targets a reality.
The typology is elegantly simple: repeating blocks of four 74–85sqm two-bedroom and 49–53sqm one-bedroom units on each level, each with a wide 10–15sqm covered deck to the north with access via an external timber stair and breezeway to the south. The top levels have raking CLT ceilings and the exterior facade features vertical, thermally-treated Abodo timber fins for screening.
The three-level design, which is less than 10m high, deliberately fits within the NZS 3604 building code, just outside “the grey zone of E2 External Moisture” by complying with the AS1 Acceptable Solution aligned with the code. The apartments also hit the so-called ‘affordable’ measure. Early in 2018, The Grounds’ one-bedroom units were selling for about $490,000 and two-bedrooms for $650,000.
Constructed offsite was a hybrid set of panels – internal pre-nailed wall frames, long XLam CLT panels for the roofs and floors (no joists required), external wall panels, including windows, TimberLab LVL and glulam posts and beams and prefabricated deck units. At The Grounds, on site construction included wall linings, suspended ceilings, long-run steel cladding, roofing, and bathroom and kitchen fit-outs.
“With prefabrication, you always want to duplicate,” says Otto. That more-or-less happened at the Housing New Zealand (HNZ) Mangere site, albeit with some improvements: the exterior panels came pre-clad and the LVL post and beam system was simplified by incorporating structure into conventional wall framing. Otto says while HNZ had done some prototyping on a complete floor and wall CLT panel system, Tallwood found conventional framing for the wall panels used about a third less material compared with a full CLT system.
In countries like Germany, there are six or seven CLT suppliers to choose from. Here there is just one – XLam – a situation set to change with Red Stag Wood Solutions announcing, in March 2018, plans for a $20-million CLT plant in Rotorua. Tallwood had planned to use untreated European CLT for The Grounds, which Otto says would have resulted in significant cost savings.
“Under certain conditions, we think you should be able to use untreated CLT for floors,” says Otto. Mainly thanks to the legacy of New Zealand’s leaky building saga, Tallwood couldn’t get that through the consent process. The other significant difference is that The Grounds sets out to expose the use of timber throughout – “trying to make a really honest building”. The HNZ building covers the timber with linings, largely to enable replacement if there is methamphetamine contamination or other damage caused by tenants.
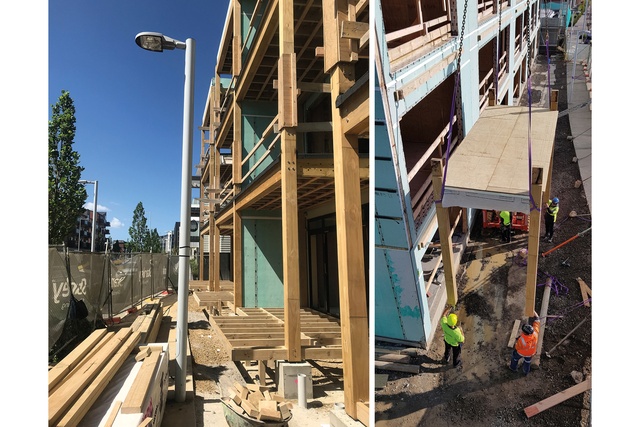
“The whole point of Tallwood is to create affordable, quality buildings at scale,” says Otto. “This typology has worked really well. Costing is good. The Grounds will be built for about $3200/sqm and, for the Mangere project, we’re expecting the same.”
Otto cites three key goals. The first and most important is certainty. “Because we know what this building is, we should know what it’s going to cost and how much material is involved.” Next is programme. “We should be aiming to build at twice the speed of a commercial build – cutting the time in half.” The third goal is quality. “It’s about having a factory environment in which there is a high level of integrity around the work – the fact it’s built in the sheltered space rather than outside.”
Otto trained in architecture, first at Unitec then at the Royal Melbourne Institute of Technology (RMIT), where he honed his strong interest in offsite manufacturing. In 2016, he and two other partners started Tallwood and, soon after, won the right to develop the Hobsonville site.
It took on the role of architect for the concept design, then brought Peddle Thorp, Innovate and other consultants on board. The project progressed with Tallwood in a joint venture development with Stanley Construction as the contractor and Stanley Modular as the maker of offsite components. The combination worked so well that, in 2018, Tallwood merged with Stanley Modular, which has its offsite factory in Matamata. That resulted in the new Tallwood – a building manufacturer with about 30 employees and contractors, an in-house design fabrication team and an installation team.
Peddle Thorp developed Tallwood’s concept through to consent and construction drawings and also to the ultimate stage – shop drawings for Stanley Modular to use for fabrication. However, for the HNZ project, Peddle Thorp’s involvement went only as far as producing a construction drawing set. Shop drawings were now done by Tallwood.
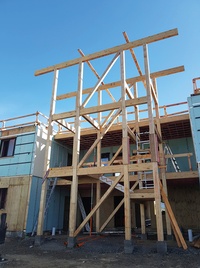
“We wanted to take responsibility for the digital construction side,” says Otto. Why? To ensure greater control and accuracy in the building process. “It’s mainly about quality control and drawings being able to be read by someone in a factory environment.” Such a shift in responsibility raises questions about just what remains to be done by the architect on site if most of the building is being fabricated in the factory. Obviously, architects want to retain their role in construction supervision to protect the design integrity but, when companies like Tallwood take over the shop drawing phase, arguably it may mean the architect’s scope of work is reduced.
So what exactly are shop drawings about? “It’s about coordination of fabrication information and that’s different from BIM (Building Information Modelling),” says Otto. “Just because you have a BIM model, that doesn’t mean you have thought about fabrication.” He’s talking about extra information like transportation requirements, which typically limit the widths of panels to a 3.3m – the height they stand when housed in an A-frame on the bed of a truck.
A growing trend in construction is an idea called digital twinning. “A digital twin is basically having a computer replica of a machine. The machine, through the ‘internet of things’ (IoT), reports back its status all the time to the digital twin. So, a BIM model of a building will show you the basic building, but it’s not a direct simulation of what the building is.”
At the Mangere site, Otto shows a sample of the shop drawings used in the factory – an incredibly precise framing set-out for a wall panel. Next to it is a table for quality assurance. “That dimension says ‘41.50 D’ so at ‘D’ (on the table) they have to measure 41.50 and any tolerance and initial it.” No room for error and, for every stick cut, there’s an audit trail of responsibility.
Tallwood’s factory isn’t particularly high tech. “We don’t have a mechanised plant. It’s basically a controlled environment with a whole lot of carpenters and a whole lot of jig tables.” That’s not to say Tallwood doesn’t want to become more mechanised to increase productivity. Obviously, that requires investment in equipment. It also needs scale. He’s talking about organisations like HNZ committing to capacity contracts – i.e. guaranteed contracted amounts over set periods – to support investment.
How many houses a year would Tallwood like to build? “We could probably do 500 now, based on our current capacity. If we wanted to do more, we’d invest in more plant, more space and a few select pieces of equipment to help increase productivity.”
Intrinsically prefab to the nth degree
“It was really just a playful idea,” says Eli Nuttall, one of five directors of Wellington-based First Light Studio. He’s referring to the ‘Flip’, the firm’s entry for PrefabNZ’s SNUG competition, which won the People’s Choice Award. The competition, to design a complementary backyard dwelling in Auckland, required a building smaller than 65sqm to meet Auckland Council’s minor dwelling definition. It also had to be made offsite and be transportable, either as a whole building or in pieces for assembly.
“To achieve a two-storey volumetric building there are all sorts of height issues when transporting it so you always have to cut the volume,” says Nuttall. “Then we thought: ‘What about having it lying on its side?’” The playful idea developed into a one-level and a two-storey version – the latter being transported on its side and literally flipped upright by crane when it arrived on site.
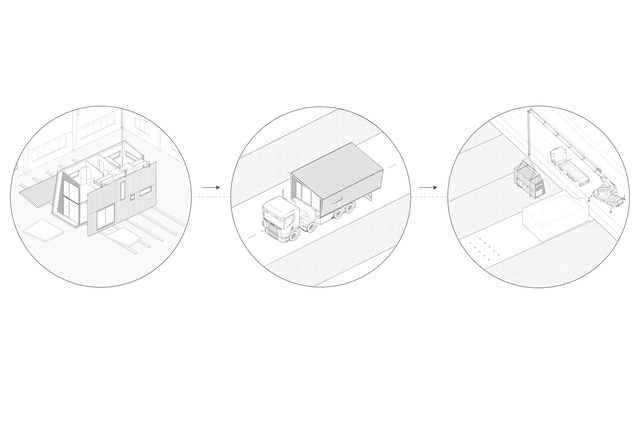
First Light has experimented a lot with prefab transportation. “You can transport things really far as long as they fit inside set transport envelope dimensions. It’s the lifting-off and putting-down procedure that’s difficult,” says Nuttall.
With volumetric houses, First Light thinks a lot about the air that is transported on the inside of the volume. “That’s part of the reason we went to a panel and pod process,” says Nuttall. “We asked: ‘What’s the minimum-sized building you need?’ Then we got rid of all the air by flat-packing the building but having pre-finished kitchens and bathrooms done as volumetric pods.”
The practice is constantly working on how to build lighter-weight panels so smaller cranes or hiabs can be used to put them into place. With its 10sqm Nook home studio, the aim is for the panels to be lifted in by hand by two people.
Which tends to make the Flip volume a bit of an anomaly. “We are in the very early start-up phase of what Flip could be. We are working on the next version of the Flip and how it becomes a sustainable entity.”
The Flip design uses Metra Construction Panels‘ panelised system – at its core a 36mm medium-density compressed fibreboard, which offers a more durable replacement for plasterboard. “We’ve used it in composite with timber framing so you get a kind of stressed skin structural panel,” adding useful robustness, says Nuttall, for transportation and flipping.
The firm is working with Auckland Council to pre-consent the construction of the Flip, so when it’s destined for an actual site, only site-related compliance is required. “We’ve yet to know what discount Auckland Council will be providing for these abbreviated consents but they will be able to process them twice as fast.” Still to be resolved is the thorny issue of infill units in Auckland attracting significant development contributions – in the order of $20,000 to $25,000 per unit – because they are deemed to be second dwellings.
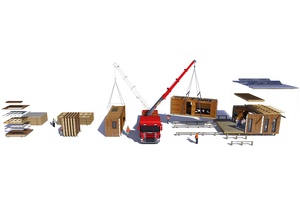
“We’d like to work with Council to reduce the development contribution to better reflect the scale of unit that’s been installed,” says Nuttall. He is hoping Council will consider the design’s in-built rainwater tanks to reduce stormwater run-off and its greywater system to minimise wastewater loads. Plus, the option of solar panels offers a contribution to the national grid. The initial estimate for the cost of the 65sqm two-bedroom Flip is $260,000 ex-factory and excluding site works and transport.
That’s still quite an expensive build but it does offer the advantage of much faster deployment of a finished building on site, plus the potential of cost reductions if the design were mass produced. Nuttall is hoping the pre-consenting process establishes a precedent for other councils to do the same and reduce costs across the board for prefabricated buildings. “I can’t see any reason why something that complies in Wellington doesn’t comply in Napier or Auckland.”
First Light Studio grew from a group of Victoria University School of Architecture students entering and winning a number of categories in 2011 in the prestigious US Department of Energy’s Solar Decathlon. While the design focus was ultimately about energy-efficient and solar-powered design, at its core it was also a prefabricated project.
“That project was intrinsically prefab to the nth degree,” says Nuttall. “We had to set it up in Wellington. Then we took it over to the States and had to assemble it within seven days. Then we had to bring it back and build it back in New Zealand for a final time.”
The First Light practice began in 2012 by re-assembling the First Light House in Wellington and opening to the public. From some 20,000 visitors, they established a client base and then set about adapting the First Light House design for a wider market with Stanley Modular. They have since sold two. “We weren’t selling dozens, but it did bring in a lot of work to the business,“ says Nuttall. “One of the learnings is that it’s very difficult to make one size fit all.”
Most of the practice’s work is in bespoke prefabricated projects, like the recently completed panel and pod trampers’ hut at a remote National Park site, incorporating a version of the firm’s UniPod – it’s winning entry in a PrefabNZ competition to design an open-source, one-piece bathroom-kitchen pod.
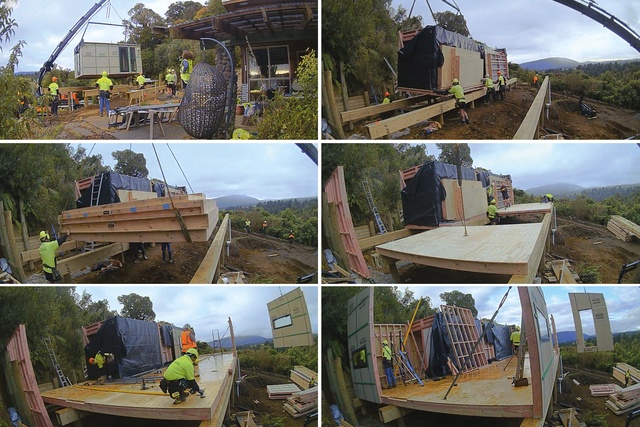
But the firm also continues to explore ways to build for a wider market. It recently collaborated with Genius Homes in Timaru to produce a new set of prefabricated designs – the Flex 90 – for the company. A key development of the process was a significant change in Genius Homes’ manufacturing, which now incorporates CLT floors into its designs.
“We are just putting together existing systems in different ways,” says Nuttall. The underlying drive in the practice is to make good architecture available to more people – providing the benefits of good design, flexible use of space, good materials, energy efficiency and thermal comfort. “A lot of these things are relatively simple to do but are missed in 95 per cent of our housing stock.”
Easier said than done. Prefabricated housing company, Matrix Homes, went into receivership in July last year. “You look at those manufacturers who have gone out on a limb when the industry is booming and we have extreme demand on housing and they have gone bust.” While Nuttall can’t shed much light on the reasons – perhaps as a result of material supply costs being so high and compliance costs increasing – he remains optimistic. “We’re going to keep trying to find the answer.”
Mass customisation at a large scale
Like First Light, Makers of Architecture was born out of a university research project. The Wellington-based practice comprises four directors, including Jae Warrander and Beth Cameron. When the members of the group graduated, they were shocked by what they found in the real world.
“First up, we asked: ‘Why are we not using these digital tools to cut buildings out and put them together?’’” says Warrander. “It seemed silly that we were doing all this accurate stuff on the computer, then we went out to the site and it was all on 2D drawings on paper that would blow away in the wind.” The group realised they needed to be present from start to finish. “That includes pricing, procurement, materials – how you delivered the drawings, in this case, digital files, to the builders.”
What it actually meant was having their own factory, which is what sets this architectural practice apart from most. Like Tallwood, it’s relatively low tech – 500sqm in an old industrial army barracks with large timber trusses and concrete floors. It has a gantry line allowing prefabricated walls to be built standing up. There’s an office pod for the computers and a Computer Numerical Control (CNC) machine for cutting plywood, kitchens, joinery and cladding cassettes.
“Fundamentally, we don’t want to do mass production but we do want to do mass customisation at a large scale,” says Cameron. “The idea is not to be exclusive in our design practice – other design practices could use this facility for building their buildings.”

The practice would like to be involved in more medium-density projects. “That is an area where some of our technologies could really create huge benefits. If we were to take on iterative development of a building typology, it could be something where there is flexibility in the result but the core logic is maintained.”
Warrander likens the process to a printer. “The computer is telling the printer to print out different words or pictures each time but the printer is doing the same process, essentially: just adjusting the colour and creating a different shape on the page.”
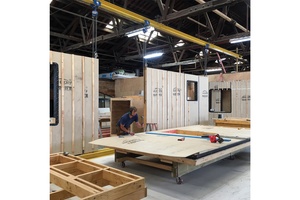
The practice is set up as two companies: Makers of Architecture is the design practice and Makers Fabrication is a separate construction company. The separation is vital for the client relationship, setting up a clear demarcation line of when the work is building and when it’s design. It also allows for great feedback between builder and designer.
Makers’ shop drawings phase involves highly detailed measurement extraction from an extremely accurate BIM model of the building. “Our drawings are also becoming more descriptive of the prefab construction and about how elements go together. Because you are working together as a team you are trying to pre-think ‘Hey that might be an issue’,” says Warrander.
Leaving the Makers factory at the time of the interview is a project called Waitarere Beach Bach, comprising hybrid panelised construction of CLT floor and roof panels with pre-framed and clad walls. Following the foundation work, all floor, roof and wall panels were assembled in just one day. Glazing was already installed on smaller openings, with most joinery frames in place to achieve weather tightness rapidly. “Typically, for a house of 140sqm, we would expect it to take around three months from start to finish,” says Cameron.
While Makers mostly does panelised construction, it recently completed a wine-tasting space called On Giants’ Shoulders, a volumetric build that the client wanted to be able to move offsite when it was no longer required. The entire structure was assembled, clad and pre-finished in the Makers Fabrication workshop before being transported to site as a complete building. On site, some glazing was installed, plus service connections were made and a rainscreen fitted.
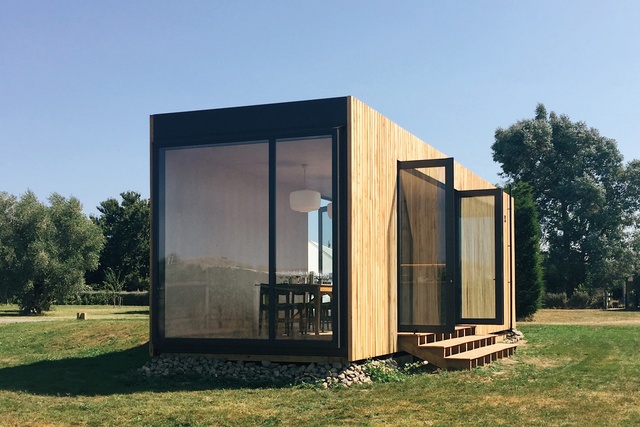
Looking to the future, Makers plans to invest in robotics. “The plan is to implement robotic arms to build a lot of the panels,” says Warrander. “When you put all the technology together, it’s probably a minimum of $2 million to get it all up and running. By putting different arms on, like a nail gun or a saw, two robots can do a whole lot of activities.” Architect as multitasking master builder.
Looking further out, has the practice ever thought of becoming a developer? “We’ve talked about it a lot. It would allow an exciting level of exploration, architecturally,” says Cameron.
“As a developer, you can say no to the real estate agent telling you what people want,” says Warrander, “and you can describe a new form of architecture.”
This article first appeared in Architecture New Zealand magazine.
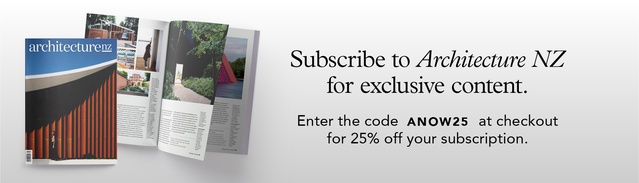