Olympic goals
In 1998, after seven years of following winter around the world, Pamela Bell achieved her goal and was the first, and only Kiwi that year, to represent New Zealand at snowboarding in the Winter Olympics.
During her years as an athlete Pamela started a clothing business, and ventured into the area of coaching. But post-Olympics, she went back to university and finished a bachelor of architecture she had started when she left school.
“Going back the second time around was different. I had a completely different perspective,” Pamela said. “After starting a snowboard clothing company while I was snowboarding as an athlete, I was more interested in the business and marketing aspects of design. That’s where my interest in prefabrication started.”
Pamela went on to spend a year in Tanzania where she worked for an Italian conservation-based non-government organisation. “It was the last place on earth I thought I would end up going but it was interesting … the building was very prosaic,” she said. “It really put a different slant on life and made me miss design. We lived in the best house in the small village. It was a three-bedroom un-reinforced concrete house with intermittent hot water and occasional electricity.”
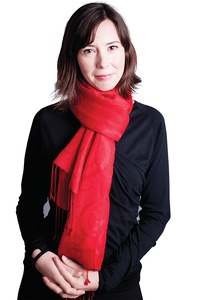
During her year in Tanzania Pamela planned her master of architecture thesis, which would eventually take her from Kaitaia to Wanaka researching the history of prefabrication, and developing an overall view of the industry in New Zealand. “There wasn’t any research on the local prefabrication indsutry to draw on so I had to go out and do it all myself,” she said.
The completed thesis provided 14 recommendations to industry about prefabrication, and has recently been turned into a book, published by the Victoria University of Wellington, and an exhibition, which is currently showing at Puke Ariki in New Plymouth.
“I wanted to test my research on the industry so I invited people to a workshop … 140 people from around the country turned up and it was evident there was this undercurrent, people were really interested in prefab but they weren’t specifying it because they simply didn’t know enough about it,” she said.
At the workshop in early 2010 it was unanimously decided a peak body was needed and a steering group was formed. “By July 2010 that group became a board and PrefabNZ became an incorporated society. I became the CEO.”
Pamela has her sights set firmly on developing the future of prefabrication in New Zealand, and sees it as a golden opportunity for the construction industry.
The society originally had a long-term plan to educate and inform industry about the benefits of prefabrication, and had an initial aim of increasing the use of prefabricated elements in building from the 17 per cent it stood at in 2010, to 40 per cent by 2020. “But a couple of months later the first Canterbury earthquake struck and our 20 year plan became an as-soon-as-possible-plan,” Pamela said.
“By February 2011 it became apparent prefab was being tarred with the same old brush … it was going to become a temporary solution.”
PrefabNZ, with Pamela at its helm, is now working to change the old association between prefabrication and cheap, flimsy, temporary buildings. Pamela said the opportunities prefabrication presented for the construction sector were endless; by employing the method buildings could be produced more efficiently, at a higher quality, and more sustainably than by utilising traditional building methods.
“About 20 per cent of New Zealand homes are prefabricated, and more than 95 per cent of new homes use pre-built wall frames and/or roof trusses,” she said. “The main advantage of prefabrication is better quality. Components, panels and modules are all created off-site, inside, and are therefore more weather-tight and provide a better thermal envelope,” she said.
“Off-site prefabrication also allows better waste management solutions, better value for the client, and reduced health and safety concerns at site.” Another benefit of prefabrication, Pamela said, was the speed of construction, which translated to less disruption around sites.
Fascinated with it since her undergraduate days, Pamela believes prefab is at the intersection of design and business, and presents considerable opportunities for the construction sector to produce large numbers of high-quality buildings in short timeframes.
“We are trying to educate people about prefab … there is a lot of focus on the social driver of creating affordable architecture. Prefab can achieve this, and provide more options for more people. Since 2000 there has also been a resurgence in architect-designed sustainable prefabricated homes, dubbed ‘green modern prefabs’.”
PrefabNZ opened HIVE, the Home Innovation Village, at Christchurch’s Canterbury Agricultural Park in April last year. “HIVE is showcasing permanent prefab solutions. We worked with the New Zealand Green Building Council (NZGBC) for Homestar ratings, and with Lifetime Design for Lifemark ratings.”
Stage one of HIVE included four homes, and has consistently attracted 300 to 400 visitors every week since it opened. Stage two, which includes the WarmFrame house, a proposed eight homestar-rated prefab dwelling, opened before Christmas.
An exhibition running concurrently at Puke Ariki in New Plymouth, Kiwi Prefab: Cottage to Cutting Edge, is an overview of past, present and future prefabricated housing, based on Pamela’s thesis, and is another way to get people thinking about prefabrication and its many benefits including shorter construction periods, affordability and sustainability, and digital fabrication use in the future, Pamela said.
“Prefabrication is an agent for change. It provides a solution particularly relevant to what is happening in New Zealand today with the shortage of houses in Auckland and Christchurch. It is a way of responding to crises where there are a huge number of houses needed in a short time. A big part of my work is education. It is about letting people know what their options are and showing people prefab in all different shapes and sizes. Prefab is not just a box on the back of a truck.”
Pamela’s vision for the future is one where prefabrication is a far more developed and widespread method of construction; an innovative, sustainable and permanent solution.
Pamela lives in Wellington with ecologist Tim Park, and her two daughters, Sophie, 6, and Tessa, 3.