Learning from Lego and Minecraft
Bill McKay investigates the modular construction used at 1243 Great North Road, in Auckland’s Point Chevalier. The Kāinga Ora project providing 61 dwellings for over-55-year-olds, was designed by Paul Brown & Associates.
I’m increasingly interested in how buildings are done these days — the way they are made rather than the way they look. Of course, their appearance, how they are to live in and so on are still crucially important but we live in times where we need to innovate. The old ways of doing things just aren’t serving the needs of many in society any more. Slow, expensive, often wasteful, sometimes leaky, increasingly unsustainable, vulnerable to climate change — the list goes on and we haven’t even touched on the human, family, social and cultural diversity of these days. It is complicated, isn’t it? Well, your construction choices are getting more complicated as well.
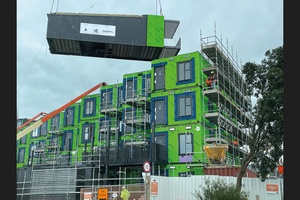
Many of us have seen this building going up in Auckland’s Point Chevalier. It’s on a prominent site, adjacent to Great North Road and the North-western Motorway. You couldn’t miss it as cranes stacked more than 60 bright-green modules in a five-to-six-storey-high pile. The locals had plenty of conversation about it — “it’s big!” (yes), “it’s bright green!” (the eye-catching building wrap before the cladding went on) and, mostly, “you won’t catch me living in a container/box”, etc. But we don’t moan about houses built out of sticks, which is what our customary way of timber-framed house-building amounts to, with heaping helpings of cement, steel, aluminium, paper and plastic to assist in strapping everything together and keeping the weather out.
I mentioned this building to a highly ranked colleague at our school of architecture and he cut me off, ranting about it being the architectural equivalent of Temu or Shein — those cut-price outfits that can channel to you astonishingly cheap stuff from the vast industrial caverns of China. I wonder if my colleague thinks the same of the more-expensive cars, whiteware and other technology we get from parts of Asia, India and elsewhere in the world where underpaid, overworked serfs are part of the work-chain. There is a double standard here; all of us liberal, middle-class folk can afford to take the moral high ground on crappy, cheap imports we don’t really need or fast fashion we can afford to ignore but we all still have smartphones in our pockets despite suspicions there could well be some slave labour in the component supply chain.
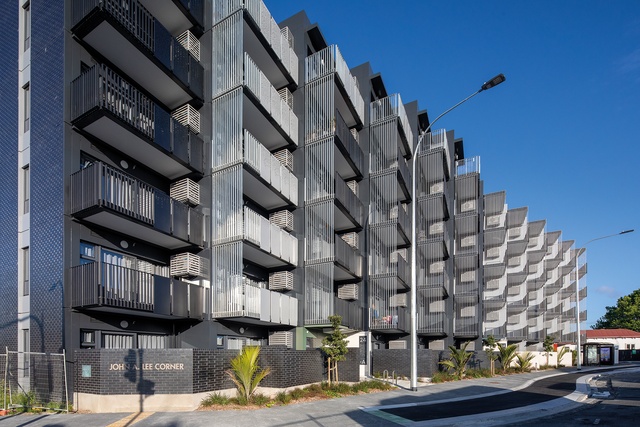
So, what is this building that’s probably generated more public conversation about architecture than the NZIA Awards ever do? It’s a Kāinga Ora project that is providing 61 dwellings for over 55-year-olds. It’s replaced a bunch of pokey pensioner flats, beyond their use-by date, on a site known as John A Lee Corner, after the famous First Labour Government under-secretary. He was responsible (with James Fletcher) for that famous swathe of state houses in the 1930s and ’40s; and, by the way, these had some innovative standardisation such as windows. The architect on this project was Paul Brown & Associates (PB&A), although a different architect was initially involved. And there were a few builders involved, including Tawera Group, which handled the steel module construction but wasn’t the builder in the traditional sense. Yes, it’s getting complicated again (it’s a theme these days); when we industrialise architectural production, who is the author?
Standing in one of the 60-something apartments here, you wouldn’t know what it was made out of. The modules don’t feel like industrial components from the inside. Each one has one bedroom (west-facing) and an accessible bathroom. Everything in here was made in China, including fittings, plumbing, interior finishes, carpet… The kitchen, living area and balcony face east towards the Point Chev shops across the road. This place is really well placed: near shops, doctors, chemist, supermarket, bus routes and so on. The old Point Chev library is moribund but about to be replaced with a medium-term solution: a ‘Mod Library’ built out of guess what? Steel modules. The world is learning from Lego and Minecraft.
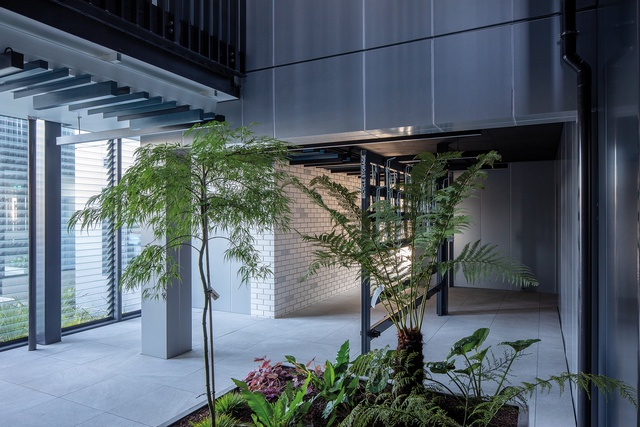
Beyond construction methodology, what else can I say about this room, this home? The sun and view are good and there is enough space. The module stacking method works well, I’m told, to improve inter-tenancy acoustics, as the sandwich of materials and air reduces sound transmission. Walking out the door, to the west, there are three lift and stair lobbies spread across the building and that’s great for us over-55s. But all this lobby area, while sheltered, is open air, and since this building sits on a ridge, it is exposed to cold south-west weather and draughty. Downstairs, on the ground floor, two modules have been interconnected and turned into a communal space for people in the building to get together. It gets sun from the eastern side and, to the west, opens to a large and also sunny garden area, which allows fruit, vegetable and herb-growing. What’s this building look like from the outside? Its stepped arrangement does reveal its mechanistic origin as stacked modules but it doesn’t look that different from a ‘traditionally’ constructed building. I’m a fan of black but it is a bit looming and gloomy when backlit by afternoon sun.
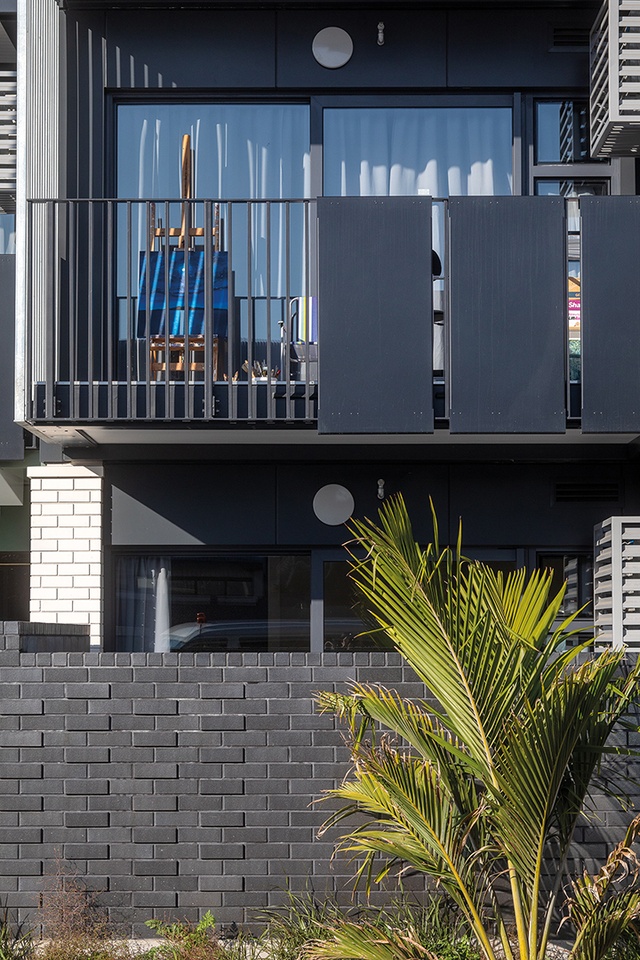
Given virtually everything has been assembled in China, I was interested in tricky things like gaining certification from New Zealand authorities, factory security, transportation, ability of modules to sit in weather and lots of other practical issues. Given a lot of political narrative at the moment, it was good to hear that the architects talked to Council early and officials were travelling to China to authorise stuff, that an internationally accredited organisation tested parts, that we had people on site to observe everything, that there were sealed-off parts of the factory where our stuff was stored, and so on. That green wrap on the modules can survive only a certain period in transit, so Tawera is talking to the factory about ‘extended shelf life’, should modules be delayed in transit or spend time in a port, paddock or car park before installation of roofing, cladding and so on. I also wondered how high you could go with a pile of modules and whether the bottom ones had extra structure added. It seems you can deal with that by a millimetre or so thickening of the module skin, so there’s no problem for a medium-rise pile. How do you tie this pile of boxes together? The tolerances for the crane to lower them on to one another are amazing — a couple of mil again, then you peel up a corner of carpet to do the bolts up. It’s not so different from how we build cars, ships, planes and so on. But it’s new to housing and how will it do in our country’s conditions? I travel a lot in the Pacific and have seen many Chinese-designed and constructed buildings falling apart after 10 years. Was my colleague at uni right? Is this cheap stuff from Asia that won’t last and explodes our carbon footprint in the process?
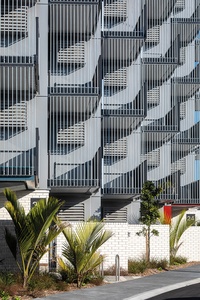
Well, we know that anything prefabricated, made in a factory, cuts down on waste, so that’s a start. The precision of factory-made modules means they can go together more quickly on site, saving time and exposure to weather. We also avoid the tangle of tradies tripping over one another on site. With a change in government, Kāinga Ora has had a lot of flak but, actually, it has built a hell of a lot of houses in the past few years and, what’s more, experimented with construction methods. Both of those are what we had to do and still need to do. And, yes, the history of the design of medium-density apartment buildings in New Zealand’s social housing has often overstretched to the point of failure but we need to innovate. And a modular system can be more complex than it sounds — there are actually 24 variations here, such as handing (left hand, right hand) or colour. There is only so much fascinating inside info that I can squeeze in here, so I urge you NZIA and ADNZ members to sort out some CPD on this topic. It is really interesting, and I strongly suspect that it’s one of the many and varied futures we need to contemplate as a profession.
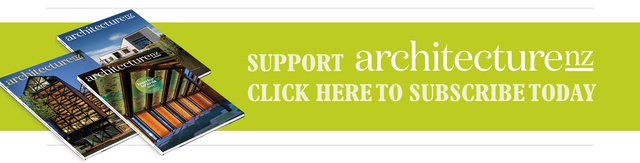