Design People: Olivia Smith
An early obsession with tying knots ultimately led to the creation of ethical hand-woven rug company Nodi. Olivia Smith shares her journey with Amanda Harkness.
Amanda Harkness (AH): What was your design training?
Olivia Smith (OS): I’ve always loved tactile things. That started from tying children’s shoelaces at kindergarten – Mum would come to pick me up and there would be a line of kids because I was the one who had learnt to tie shoelaces early. At home, my mum did cross stitch and my nan did quilting but I also just had a real fascination with irregular texture.
I started a degree in fashion and textile design at Massey in Wellington and studied for 18 months before deciding to move to Milan to au pair, learn Italian and, generally, just cruise around Europe.
After a year of au-pairing, I wanted to study again so I found a year-long diploma in fashion and textile design at Milan’s Institute of European Design. Ironically, I failed the weaving paper but I gained a deep appreciation for how to weave things. It takes a lot of time and incredible patience – you have to be meticulous.
AH: After you finished your studies, what did you do?
OS: You need to do an internship to complete your course so I spent a year as an intern in Milan. I worked at an atelier with an American woman who was importing hand-block-printed textiles out of India. I found that fascinating and it gave me insight into a world where they were creating things by hand with unique end results.
When my visa expired, I moved to Sydney and worked for Camerich in Waterloo, selling furniture and rugs to interior designers and architects. We launched the Fendi Home and Kenzo Maison brands and that connected me to rugs. I was drawn to their tactile nature and irregular textures and finishes. I loved selling them more than selling furniture.
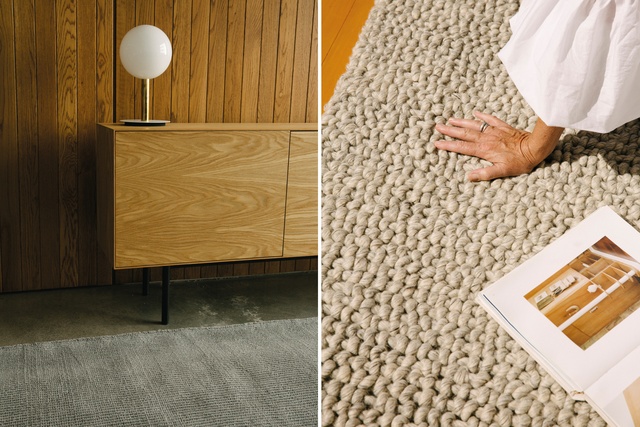
AH: What inspired you to venture to India?
OS: After three years in Sydney, I decided to move to India and explore how they make rugs, not really with the thought of starting a business but just to feed my curiosity. I was 25 and at an age when I could throw myself into things. Initially, I went to Delhi and I met with a quality control agent who led me to a number of different factories around India – in Panipat, Jaipur and Bedori.
AH: How did you go about learning the craft?
OS: I took loads of videos and photos to learn how to make a rug by hand, from the raw fibre through to the finished product, using their traditional weaving techniques. The factories I visited ranged in size: some with just 10 looms set up and others with up to 600 staff. The weavers don’t speak English but the factory owners explained things.
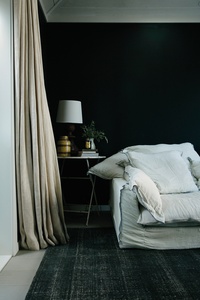
There’s a head of production at each stage of the process – dying, spinning the yarn, weaving and finishing – they’re called the masters. Men often do the heavy lifting and weaving work, and the women do a lot of the finishing, using handmade shears to finish the rugs by hand. The loose tufts need to be clipped, so they hand surge the edges with large needles and yarn, and then they go along, row by row, clipping.
AH: How was Nodi born?
OS: After a couple of months in India, I chose a family-run, GoodWeave-certified, ethical factory and gave them some of my designs to weave. They did a couple of prototypes and then shipped them to me on my return to Wellington and, when these huge, heavy rugs landed on my doorstep, I thought: What have I done? I had been creating hand-knotted fabric necklaces to make some extra money when I was interning in Milan. That’s where I learnt the word ‘nodi’, meaning ‘knots’ in Italian, so I had the Nodi brand sitting in the back of my mind.
I produced a catalogue and rented a space off Cuba Street for a week. I hung the rugs and invited everyone I knew to a launch party, and then started selling to family and friends and picking up retailers. That was five years ago, in early 2014.
The collection, called Jaipur Doors, was heavily inspired by my time in India and by the Hawa Mahal palace in Jaipur. It was made up of five very colourful designs and nine different sizes, which was just crazy. I didn’t hold any stock – they were all custom-ordered with an eight-to-10 week turnaround. I continued with the business when I moved to Mount Maunganui, working from an outdoor shed; then, I moved to Auckland and worked on my dining room table. I was really focused on wholesale at that stage. After three years, I moved into a shared space on K Road for a year and then to here, in Parnell, where we’ve been for a year.
AH: Who do you sell to now?
OS: We have our own store here in Faraday Street, as well as selling to high-end homeware boutique retailers – Tessuti in Auckland and Precinct 35 in Wellington. Over the last five years, we’ve built up a strong business with trade through interior designers and architects. And we now work with the top architects both here and in North America.
North America has been a real focus over the last six months, following a one-month pop-up with Resident in New York during ICFF (the international furniture design fair). The States was always part of the plan so that was really great timing. We’re now working on establishing some strong relationships with key accounts in North America.
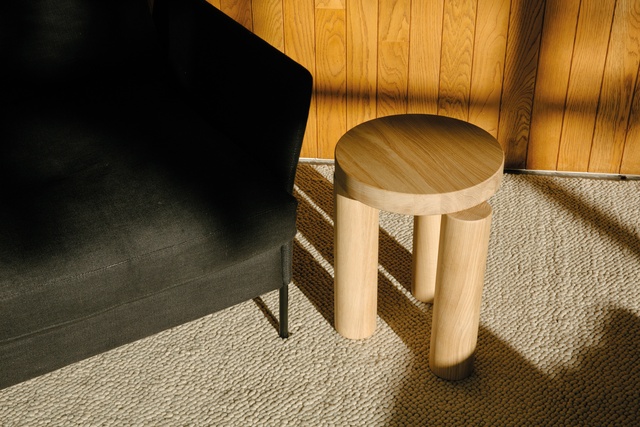
AH: What inspires your new collections?
OS: There’s a big movement around natural, handmade, sustainable and fair-trade at the moment, and it’s what we do. A lot of the rugs begin with the handspun yarn – it’s a really unique, beautiful yarn, which is thick and thin and slightly hairy. When I was last in India, I went to West Bengal, where they grow the jute, and explored the whole process of how it’s grown, how they extract the yarn and how they spin it.
We started to introduce different factories after about two years because they all specialise in different techniques. We produce rugs with New Zealand and Himalayan wool and we do flat-woven, chunky and hand-knotted jute. We also have flat-woven woollen rugs and chunky felted wool rugs. We’re often asked to do wall-to-wall carpet and large rugs.
Our latest releases are in a really soft, pure wool and a bamboo silk – we wanted a new texture that was slightly elevated and more luxurious, so we started sampling it and showing it to designers and they really loved it.
AH: What lies ahead for you and the industry?
OS: People, both young and old, are becoming more conscious about how they consume and they’re really interested in wearability and purchasing something that lasts; this is why we’re constantly working on creating a durable, quality product. My house is full of rugs so we live with them. There are different weaves that suit different environments and we try to guide people through that so they select the right rug, which they will hopefully enjoy underfoot for a very long time.
This article first appeared in Houses magazine.
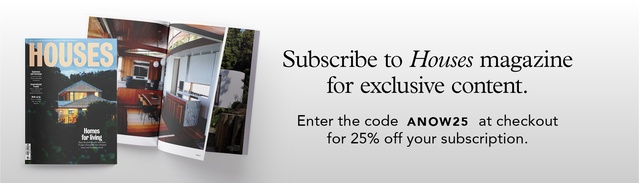