Breathing new life into recovered building materials
Partner content: After the Kaikoura earthquake, several Wellington seafront buildings were scheduled for demolition. Destined for landfill, Thermosash disassembled a seven-year-old façade for reuse in other projects.
This is a story of recovery and reuse, and the resultant elimination of waste and reduction in CO2 emissions – a positive step towards achieving a sustainable, circular economy.
April 2009 marked the completion of the BNZ Harbour Quays building on Wellington’s waterfront. Featuring a Thermosash total clad curtainwall system, the new, high profile building became the Bank of New Zealand’s flagship headquarters. Due to its siting on reclaimed land, Thermosash worked with the design team early in the development and assisted in generating several unique features to help reduce weight on the façade and therefore to the overall structure. The project architects had proposed a three-dimensional façade element in precast concrete.
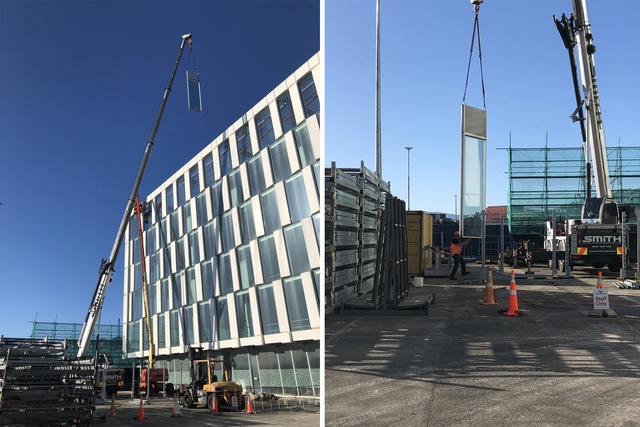
The staggered panel design introduced a significant number of junctions between the proposed precast elements and the vision panels on the north and south elevations. In order to improve the weathertightness and increase the speed of construction on site, Thermosash proposed replicating the 3D elements in light-weight pressed metal and ‘hanging’ them in front of a continuous unitised panel wall curtainwall, thereby reducing the weight and mitigating potential weather tightness and building movement issues. During manufacturing, these 3D elements came to be known as the ‘bathtubs’, due to their distinctive moulded profile.
The Kaikoura earthquake struck with such magnitude in November 2016 that it caused damage to a significant number of buildings in the greater Wellington area. The reclaimed land below many of the buildings around the seafront suffered from the impact, resulting in extensive structural damage.
Thankfully – and to the credit of the engineers – despite the damage, none of the buildings collapsed, and injuries were limited. In the months following the earthquake, the BNZ Harbour Quays building was one of 20 deemed unsafe to reoccupy and was eventually marked for demolition.
One of the many advantages of a unitised façade is that it assembles like Lego parts, which means it can be disassembled almost as easily. CentrePort was focused on recycling as much of the building as possible, as well as ensuring the demolition was undertaken in a safe manner due to its vicinity to a fully operational port, adjacent to the Bluebridge ferry terminal and a major thoroughfare into Wellington’s CBD. With a contract in place, CentrePort and Ceres Demolition worked diligently towards the demolition of the BNZ Harbour Quays building that would include salvaging the virtually undamaged and entirely reusable Thermosash façade system.
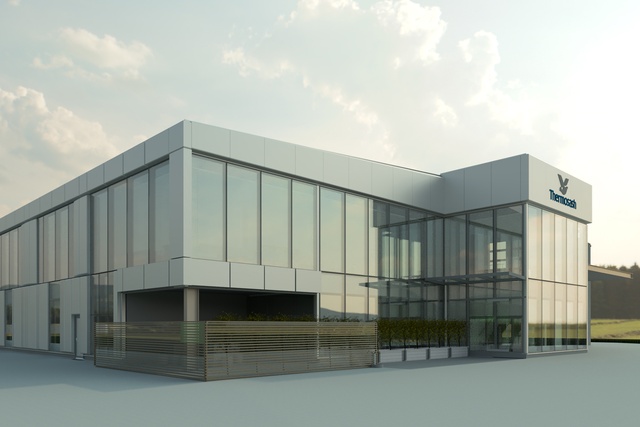
Thermosash undertook the removal of the unitised panels and was able to provide the upcycled, prefabricated façade panels to planned future projects, including the Wellington Children’s Hospital link bridge and the new Thermosash factory and office building in Levin. Additional panels are scheduled for use on a proposed new Thermosash Auckland office and factory development.
Thermosash Wellington Area Manager, Dave Rooker sees the outcome of the BNZ Harbour Quays demolition as an encouraging first for the construction industry. “The panels were on the building for only seven of their projected 50-year plus potential life,” he says. “It’s easy to see the benefits of recycling the primary materials we use every day in aluminium and glass, yet, as far as I’m aware, this is the first opportunity of the upcycling of a full façade system in New Zealand.”
Contact Thermosash for more information:
Auckland – 09 444 4944
Wellington – 04 939 4500
Christchurch – 03 348 4004
ArchitectureNow works with a range of partners in the A&D supply sector to source appropriate content for the site. This article has been supported by Thermosash.