BRANZ HQ gets a makeover
BRANZ headquarters in Wellington has undergone its first major makeover and expansion in 20 years.
To get to the new Building Research Association of New Zealand (BRANZ) headquarters from Hutt Valley, go up and over the Hayward Hill, turn off at Moonshine Road and wind along through farmland to number 1332.
Being out in the sticks makes a decent cafeteria essential, along with independent firefighting capability (many tanks of water) and a stand-alone sewerage system. The remoteness of the site and the nature of BRANZ’s work have been factors in the sequencing of construction, in health and safety and security measures, and waste management. While BRANZ is using best practice techniques and information, the new Nikau building will be of interest.
Nikau is built according to Structural Timber Innovation Company (STIC) engineering principles that involve innovative large-span timber building technologies primarily for use in non-residential buildings. It is considered a sustainable building for the future.
The BMS system, server and lab security are also state of the art. The refurbishment, budgeted at $11.4m, began in August 2010, and is the first major improvement to the campus for over 20 years. The site remains fully operational during construction so it’s a testing time for contractor Fletcher Construction, architects Warren and Mahoney and staff at BRANZ.
Flexibility is a key requirement and clear, frequent communication through staff and refurbishment committee meetings, staff emails, newsletters, site tours and CEO blogs. The occasional Friday afternoon ‘Fletcher Challenge’ sees BRANZ and contractors square off in table tennis, pool and cricket, which gives them a taste of BRANZ’s culture. Here they make their own fun. The interiors of existing buildings, which contain workshops, laboratories and administration areas, are being reconfigured and modernised.
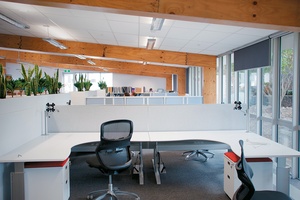
No more low ceilings, dark wood interiors and artificial light. Going, gone, the old-fashioned green carpet that shouts 1970s along a ‘rabbit warren’ of corridors and offices through Totara building. Labs and offices in various buildings will be opened out, some ceilings raised, existing buildings stripped back and brought up to code. The exterior will be upgraded with most of the campus footprint remaining the same and the physical links between areas will create better communal space for staff and visitors.
The new stand-alone Nikau building and two additional spaces have been completed already and integrated with the existing buildings. A new cafetaria will be part of the social hub between Rimu and Totara building. Totara will become an open plan office space with meeting and communal areas, and a new entrance created on the south side. Ceiling space will be opened and passive design features incorporated including natural ventilation and solar panelling. A pellet/woodchip boiler that uses a carbon neutral, renewable fuel source will heat water in radiators and help lower BRANZ’s carbon footprint.
A site visit in April began around the new water tanks – a first priority was to maintain coverage as the tanks replace a single 82,000 litre tank removed from the Nikau building site. Tane Graham, Fletcher Construction’s Project Manager and Jack Lyons, BRANZ Building Controls and Facilities Manager, talked about staff induction and some peculiarities of the site. The contractor has its own toilets and waste management system. Human and liquid site waste (paint, detergent, chemicals) is removed every week to avoid upsetting the balance of BRANZ’s custom-built sewerage plant. Solid building waste that’s tracked – a stipulated 90 per cent – goes into labeled containers for recycling and disposal.
Staff induction for contractors and BRANZ has involved new health and safety measures. Fletcher Construction and subcontractors get the lowdown on the special nature of the testing facility. No photographs allowed, no touching – a breakage could destroy 10 years’ work, and beware of chemicals. BRANZ staff have been inducted into Fletcher’s requirements and issued with hard hats and high-visibility gear for times they are inside a construction area. Rimu building has been in various stages of demolition and rebuilding.

Within this building BRANZ carries out a a range of testing from weathertightness in a wet area laboratory, materials performance and durability testing through to insulation testing within the thermal laboratory. This lab is specially designed with double-layered, fully insulated walls to keep temperature and humidity controlled for a range of product testing using sophisticated equipment. Some labs were operational, in others linings and plastering were in process or aluminium partitioning going up. In another area mezzanine floors had come down and the work spaces expanded.
Work for BRANZ and contractors has been a movable feast with temporary areas prepared ahead, equipment and staff shifted, then returned once the home space had been refurbished. Rimu has been taken back to frame and slab, the old insulation replaced with R-5; thermally broken double-glazing in new aluminium frames; a new metal, LT7 roof installed over the existing roof to keep the building space live. Clear communication and the ability to compromise is essential. “Planning always gets spanners in the works,” Mr Graham said. “It’s a bit like sailing, you’ve got to adapt and change tack every now and then. You can’t go this way so you go that way.”
A regular occurrence is when someone is in the middle of a test and the contractor has to change focus. “The builders want to knock something down and the test isn’t finished. You have to wait for a window of opportunity for tests to end so they can shut them down, move the equipment and fire them up again.” Tests can last for six, sometimes 15 weeks.
“We said we couldn’t have that,” Mr Graham said. “There have been some adjustments on both sides. The delivery of some new equipment also had to be delayed so we didn’t have to deal with that on site.” Fletcher Construction has invited BRANZ staff to do quick checks on their work. A check on an insulation job using a thermal imaging camera was “good for the guys,” Mr Graham said. “They can see what BRANZ does. The young apprentices see the things that can be done right in front of them. Even with the linings on the wall [the camera] can still check the insulation behind. That really got the guys nervous I think.”
And for BRANZ it’s useful to see work in action as a whole process and how it fits together. Nikau building is a light, bright, warm space to step into. The 20 metre long LVL beams are a striking feature, and very stable. A similar system was used for the Nelson Marlborough Institute of Technology building. There was some uncertainty about how long it would take to erect the structure. Mr Graham said the LVL portals went up in three days, the LVL bracing wall panels and LVL roof purlins took around two weeks once the portals were up “to make it look like a structure”.
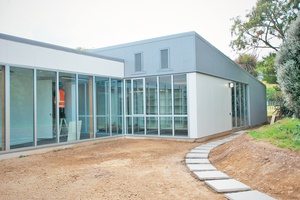
“The post tensioning of each rod took one full day to complete by BBR Contech then all of the external framing and exterior cladding got under way.” Nikau is one of the first single storey structures of its kind to be occupied in New Zealand. Roy Wilson, director, Warren and Mahoney, said this type of timber framed structure will lead the way for three to four storey buildings in the rebuilding of Christchurch. On a more general note he complimented the teamwork through, at times, “rather trying conditions”.
“Staging the construction work around the various labs and workshops, while ensuring that power and mechanical systems are kept working, has caused considerable planning and co-operation between the contractor and the BRANZ team. All have been located into new positions within the building creating a more rational planning result.” He also noted that the building had been developed and extended numerous times over the past 30 years and the building services were not very well recorded.
“I think the integration of construction work in one area required building services work in another to be able to maintain supply. For example, lighting and power in the workshop had the switchboard in a staff area miles away. Sorting all this out at the commencement of the contract caused a few anxious moments. However, all major staged completion dates have been met. It would be hoped that we now have a clear run at the Totara building, and I believe the team are keen to peg this back.”
In his still green carpeted office in Totara, BRANZ CEO Pieter Burghout was pleased the project was, so far, on time and within budget. As this is a BRANZ project he said all parties were clear they were working in “a bit of a fishbowl”. “We are going to be quite open about how it’s all gone – the way we contracted it, the way it’s been priced, the way we’ve gone through the process and the results at the end. We are treating it as a learning opportunity for ourselves and for the industry,” Mr Burghout said.
BRANZ wanted to build a good building that was going to stand the test of time, and cost was also a limiting factor. However, once it is finished he thinks the heating and cooling system could be leading the field. “Come back on a very hot or cold day and see how we are enjoying ourselves.” He said the upgrade investment of New Zealand building and construction industry’s centre for research, testing and knowledge is a strong signal that BRANZ is here to stay, that they are doing a good job and intend to continue doing so. The project is due to be completed by February 2012.
And the green carpet? It may or may not be recycled, but then who would want it? perhaps an indoor mini-golf? Marketing and communications advisor Tui MacDonald says they have given staff tiny off-cuts as a memento.
BMS and other systems
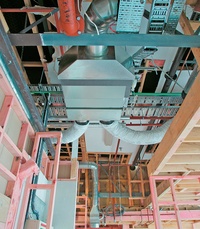
The Building Management System (BMS) will monitor and control mainly the HVAC and heating systems in the building, automatically turning the new Pellet Boiler System on to add more additional heat to the buildings if required. The BMS system is also integrated into the solar panel hot water heating system. The lights are controlled using the C-Bus Lighting Control System, which adjusts the level of light with the ambient light levels and is also on a sensor system to shut down after 20 minutes of inactivity in that room.
The exterior lighting system is integrated into the security system so if any alarms are triggered the exterior lights turn on. A fully upgraded security system has been installed with new motion sensor cameras, new access control throughout campus and a new ‘man-down’ system, which will automatically let the monitoring company know if one of the BRANZ staff in the workshop or lab that is using the system has collapsed.
So far we have created structures with structural steel and timber, concrete block, post-tensioned LVL and timber. Cladding/window systems being used are PBS Eterpan on Xpress Clad. Aluminium cavity systems, Wight Aluminium, thermally broken. Aluminium window suite with double glazed windows, VM Zinc fascia. panels with pressed metal cladding also. New R5.0 insulation is installed in the ceilings, and R2.6 insulation to a majority of the external walls.
Follow us on Twitter: @ProBuildingNZ