Behind the Object: The Wanaka tables
As part of our Behind the Object series, we take a look at the design and creation of the Wanaka tables by Yann Gandon of Mobilier Ethique. Gandon is a French designer, now residing in Auckland, who is passionate about natural and sustainable materials. The Wanaka tables are made from 91 per cent recycled materials and hand-made in Gandon's workshop in Henderson.
How did the design of these tables come about? Was it commissioned for a particular project, or did you start with an idea that you hoped to sell from there?
Yann Gandon (YG): The Wanaka tables are the first collection I released for Mobilier Ethique. I stayed in a guest house in Wanaka where the living room had windows on three sides with a view of the mountains and a river. That’s where the idea of having a table that allowed a feeling of lightness to keep the view outside came into my mind. The initial idea came to me first with the goal of getting a full set of tables that could fit in the living room. The first design was about the nesting tables, which are very interesting pieces of furniture. They could even be considered old school. I like them, though, as they can provide a purposeful space to store and showcase items while giving additional storage if required; this is a very flexible object. Hence, I wanted to have something very light and subtle. The console with a drawer came later on, following a request from an interior designer to add some storage.
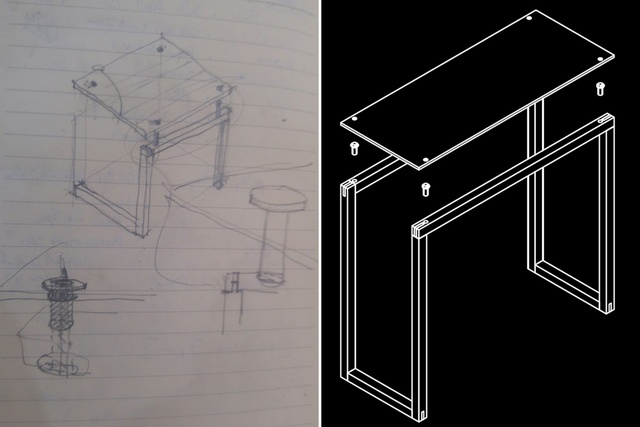
Obviously, the sustainability aspect of the tables is important to you personally. How did that play into what you wanted to achieve with this design?
YG: The idea is to show that recycled wood can be refined and not only rustic as we often see. Native recycled wood is an abundant resource in New Zealand and very often goes into landfill. It is such beautiful timber, usually from very old trees. It’s often difficult to get the same quality now. The age and the nail holes give the wood a very strong character, and by making the tables very light in nature, I wanted to give a good balance.
How did you take your initial concept from paper to reality?
YG: The inspiration came when I was learning a lot about the Bauhaus, reading and watching a lot of documentaries and trying to understand that movement. They started to use simple geometric shapes without any extra features. The first prototype was a square top in clear acrylic sheet and pocket joints to attach the legs. The pocket joints weren’t strong enough, so I needed something stronger that could also add value to the design; that’s why I added the bridle joints. There are very strong and also one the few wood joints that are visible and bring an added aesthetic value.
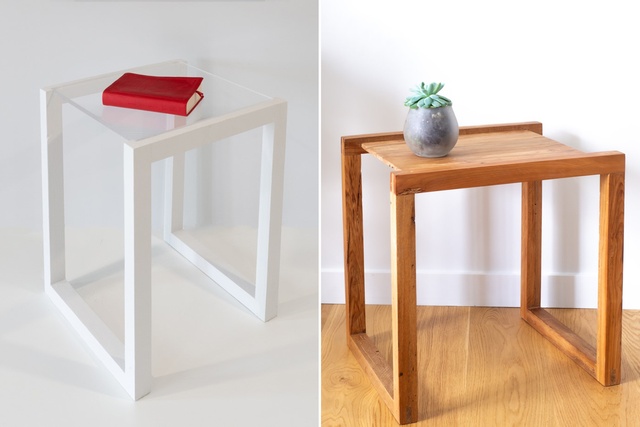
Tell me more about the ways that the process of making these tables informed the decisions around materials.
YG: The design and the making process are often interconnected, like with the decision to use a bridle joint, for example. However, the floating top and the brass support of the final design came later on. The first idea was to use glass for the top, as I was saying before. In the end, I wound up using wood for the top but still wanted a design feature that would keep that lightness. This is where I designed the brass supports and the floating top. I always had in mind to associate brass and Rimu as they are two colours that work well together.
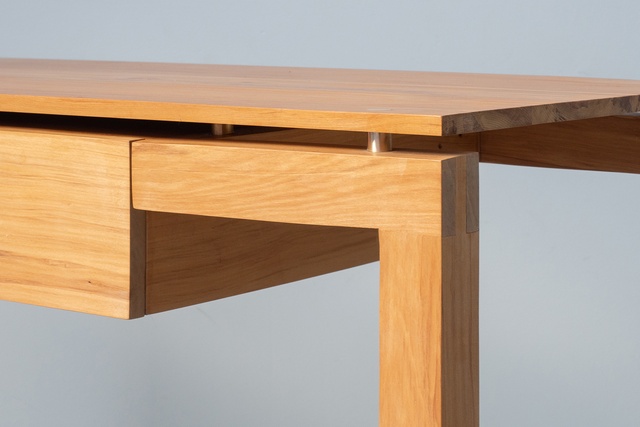
Were there any unexpected challenges when it came to manufacturing the final design? Did you have to tweak anything to make it work?
YG: Any wood joint can become challenging when you have to make them on a larger scale. I first made them on a table saw using a jig that I made. This was working but had a very long set-up time and, also, the margin of error was too high. I eventually ended up using a spindle moulder and a specific platform. This also has a long set-up time but, once it’s done, it gives a regular and high-quality joint.
How have you gone about scaling up the production of these tables? How have you held on to the sustainable aspects of the design while creating them at a larger scale?
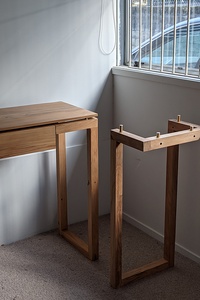
YG: Holding the sustainability aspects means almost restarting from zero. As soon as you start looking at the manufacturing process, where it has been made and if it can be recycled, it reduces a lot of the materials that can be used. As an example, the first prototype was made of a clear acrylic sheet offcut. Upcycling some offcuts is easy, but when you want to make more than one piece it becomes trickier. I had the idea, then, to use glass to keep that transparency. The glass that would be used for the top is called tempered glass. This is very durable but, unlike normal glass, it can’t be recycled as it breaks into very small pieces.
When it comes to making the tables on a larger scale, the goal is always to limit the environmental impact and carbon emissions of the table. Using native recycled wood is one of the most sustainable ways of procuring material. This is an existing material, sourced locally so the environmental impact is very low. The brass components are made with a CNC supplier in Auckland. I don’t track the brass origins as it is such small pieces. The tables are handcrafted in my workshop in Henderson, Auckland, and we deliver only in New Zealand. The overall environmental impact of the tables is very low and it shows that recycled wood can be used for fine woodworking.
See more of Yann’s work at mobilier-ethique.com and read more from the Behind the Object series here.