Behind the Object: Terraced Concrete Bowl
Furniture designer Raimana Jones of Atelier Jones details the process he used to create what he calls "a bold architectural object designed for everyday life".
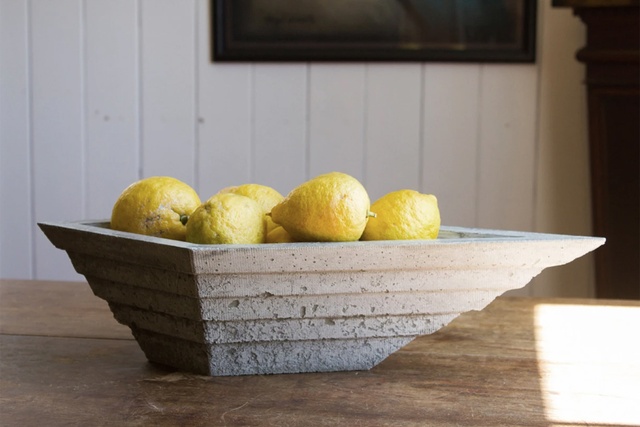
The past can be a great source of inspiration. I was looking at some of the world-renowned historical concrete architecture for inspiration for my new design project. There was a noticeable terraced geometry that I found common in both the Pantheon ceiling (126 AD) and in some of the architecture of Carlo Scarpa.
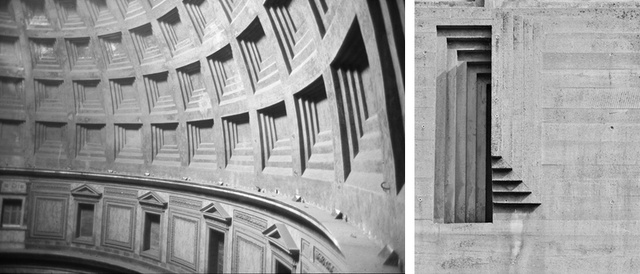
The terraced geometries add detailing and generate a beautiful, rhythmic play of shadows onto the concrete works – qualities that are monumental yet refined, present in both of these architectures. I wanted to acknowledge these qualities for the design of a fruit bowl. The brief became: Can a fruit bowl, an everyday object, be reinterpreted to generate the monumental yet refined qualities found in the Pantheon ceiling and some of Scarpa’s work?
Design and iterative process
The bowl went through three main design iterations. The first iteration was to get a sense of the overall geometries, scale and proportions of the bowl and set a good foundation around mold-making and casting. The second focused on refining the formal aesthetic and functionality of the internal volume of the bowl. The third and final one, on developing the external shell of the bowl.
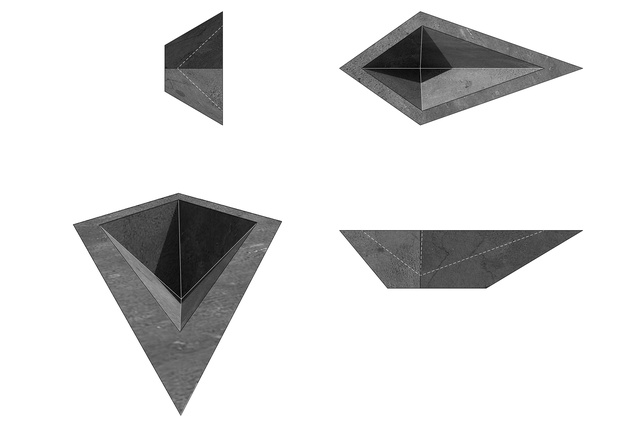
Going through this process built a good foundation around mould-making and the casting process. The next iteration involved developing the dish part of the bowl, using the precision of the CNC router technology to build the intricacies of the terraced geometries.
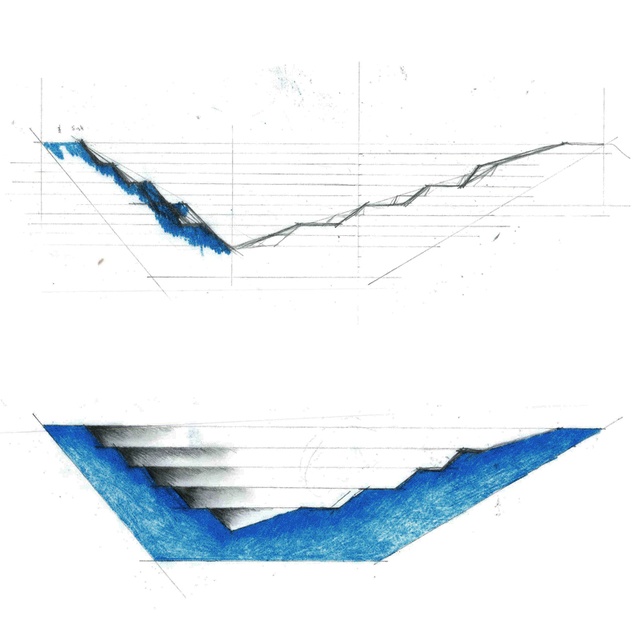
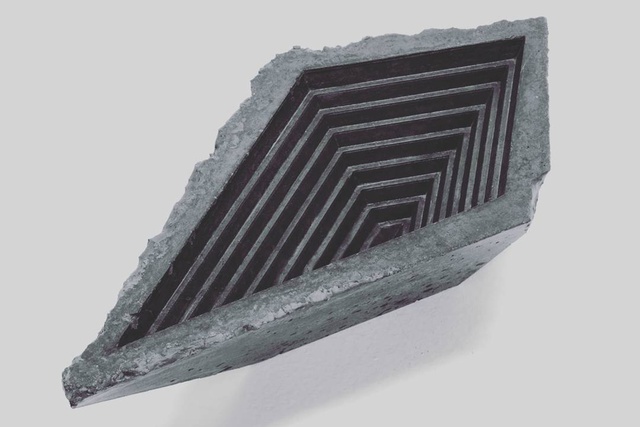
Using the CNC router proved to be a good medium for mould-making. The final iteration revolved around developing the external shell of the bowl, whilst continuing to utilise CNC routing technology.
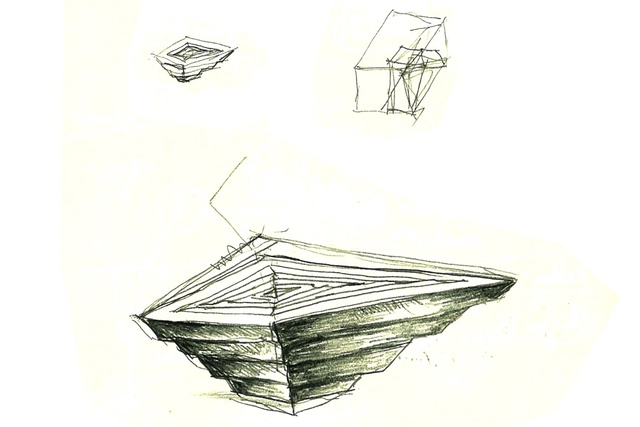
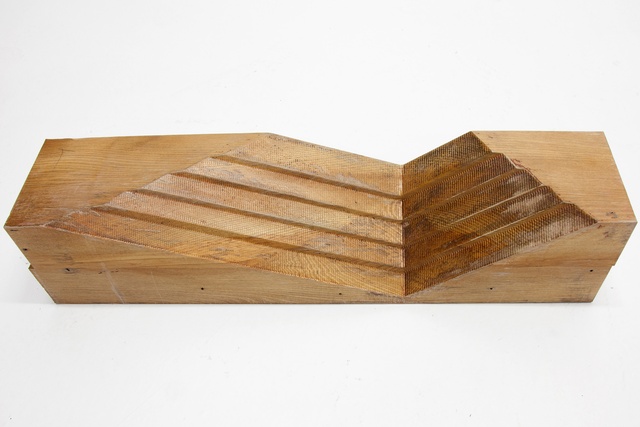
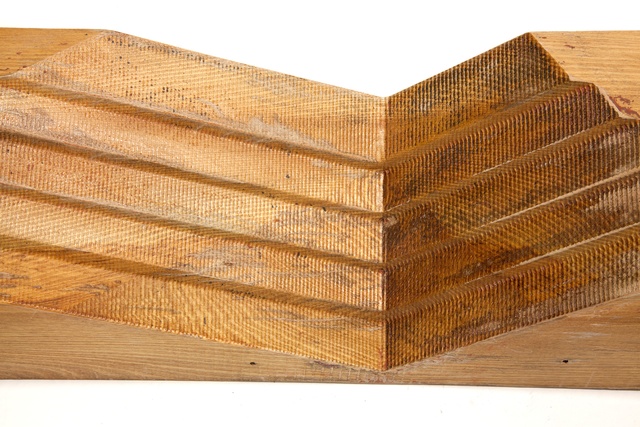
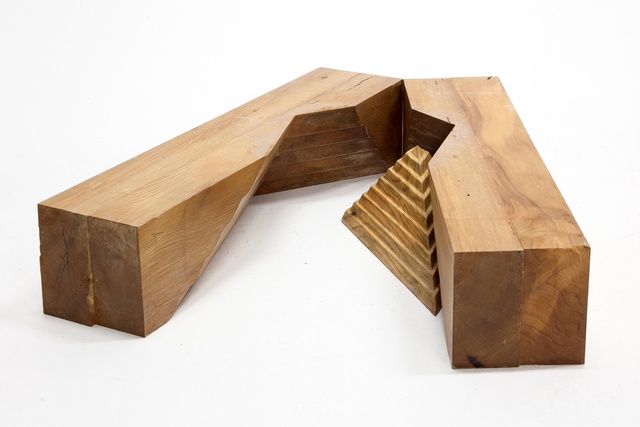
To pass from a manual to a more computerised and automated form of mould production was a good transition towards the evolution of the design of the bowl. Personally, the use of CNC routing technology has unlocked more freedom and control around complex form-making.
The section below is the step by step casting process behind the finalised version of the Terraced concrete bowl.
Casting process
1. Outer and inner mould assembly
The mould is made out of three CNC-routed, sealed solid timber parts. Two ‘negative’ carved blocks make up the outside shell of the bowl and a ‘positive’ part makes the internal terraced space.
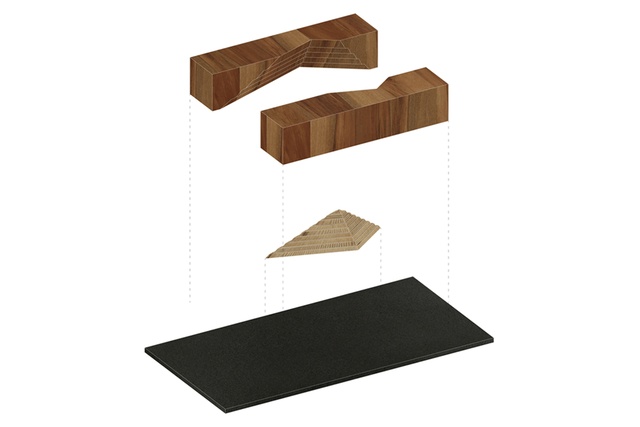
2. Fine casting mixture pour
Our concrete mixture is composed of sand, fine aggregates, portland cement, water and a binding agent, that acts as a reinforcer. Getting a good solid to liquid ratio is key to pick up fine details in the mould and preserve strength. Once the mixture is poured, the mould is vibrated to get rid of air bubbles trapped inside.
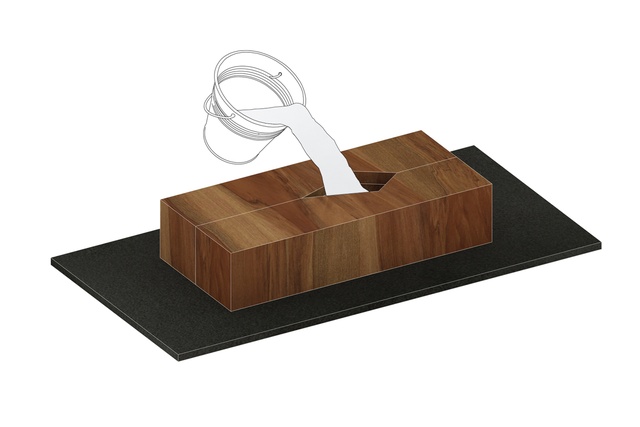
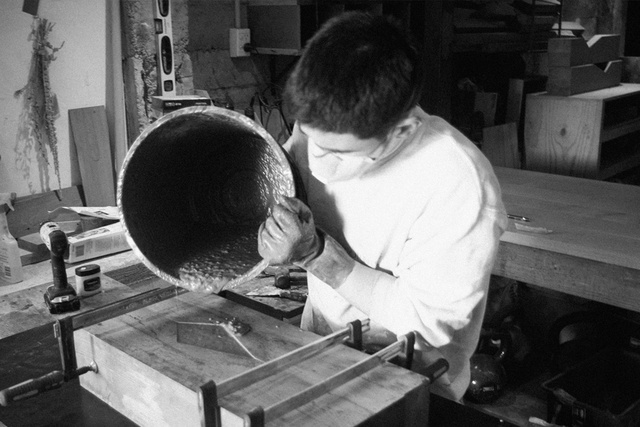
3. Outer mould disassembly
It takes about 24 hours for the casting mixture to dry. The two timber blocks that make up the external shell of the bowl are pulled apart.
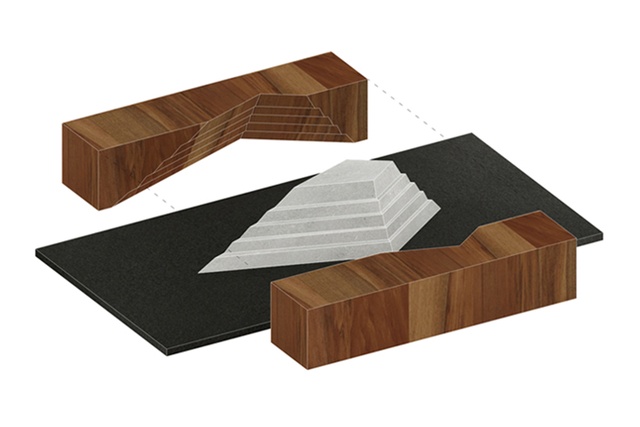
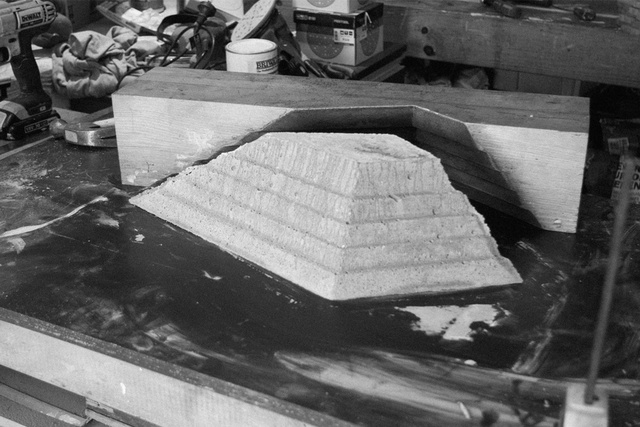
4. Inner mould disassembly
The bowl is flipped on its base and the internal positive part is removed.
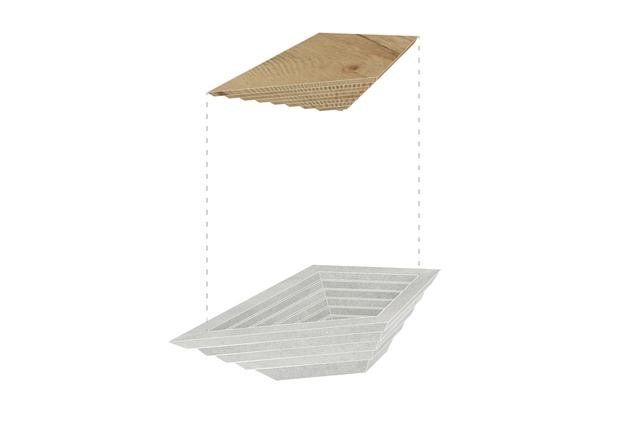
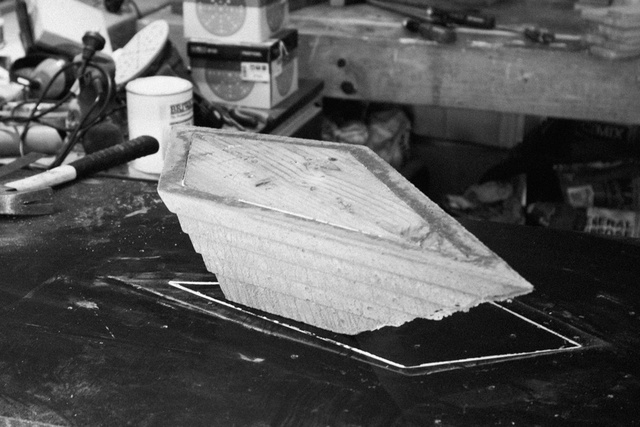
Once all the mould parts have been successfully removed, the sharp edges of the bowl are hand-sanded it is finally coated with a waterproof sealer.
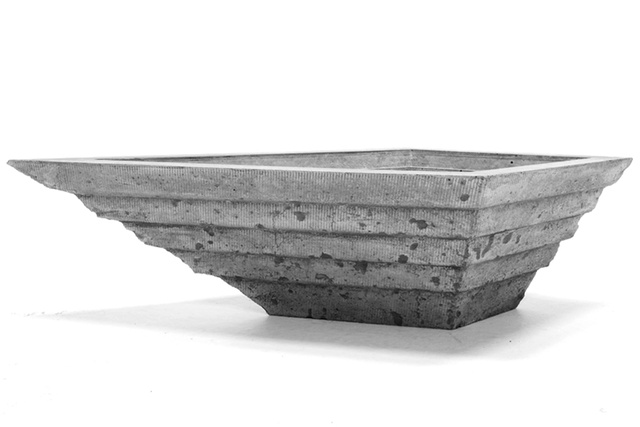
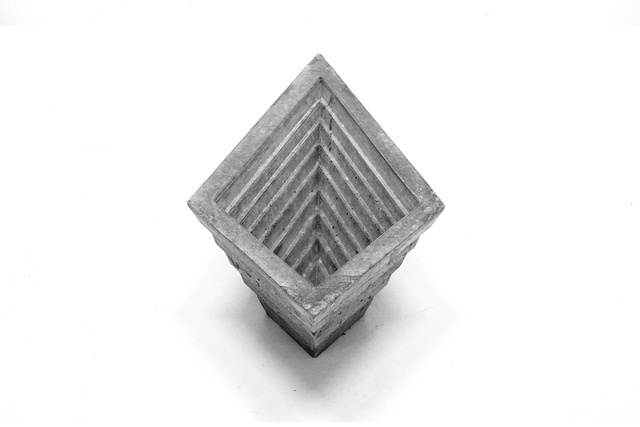
The monumental yet refined qualities of the Pantheon and Scarpa’s architecture have been captured and injected into a small-scale object. The result is a bold architectural object designed for everyday life.
A big thank you to sculptress Shona Lyon, technician and designer Harold Barton and ceramicist Harriet Stockman for their guidance throughout this process.
This article first appeared on atelierjonesdesign.co.nz.
See more from the Behind the Object series here.