Accounting for carbon
Amanda Harkness investigates Studio Pacific Architecture’s adaptive re-use of Brandon House and finds a makeover that delivers the commercial tower, dating back to the 1960s, some impressive sustainability credentials.
They say people often look like their dogs. I wonder if the same can be said of building owners. There’s something quintessentially Bob Jones about his latest acquisition on Featherston Street – its bronze-glazed façade, red marble podium and leathered lift doors – and that’s all before we even hear the Mozart playlist being piped through the lobby. It’s easy to imagine Sir Bob pulling up outside in a honey coloured Bentley to survey what is now, undoubtedly, one of the best-looking buildings on the row.
But what we might not grasp at first glance is that this shining tower is an incredible story of re-use – just the type of story that would make the climate-crusading, Pritzker Prize-winning architect Anne Lacaton’s heart sing. Reuse, recycle, refurbish, renovate but never, ever, demolish. And, to give him his due, this, too, is the preferred model of the outspoken former boxer, short-term politician and long-term developer as he builds and maintains his property empire in the capital city and beyond.
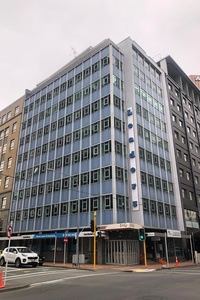
Ironically, this particular project was destined to face the wrecker’s ball. A 1960s’ commercial office building, hitting the golden fit-for-purpose age of 60, it was at approximately 50 per cent of NBS (new building standard) for seismic resilience. This was not financially insurmountable but asbestos around the windows, on top of the required restrengthening, called for the removal and replacement of the entire façade.
Sir Bob, who had already employed the services of the climate-conscious Studio Pacific Architecture, asked the practice to design for him a tall timber tower. The architects jumped at the opportunity and took detailed drawings through to building consent but the resulting cost was more than Robert Jones Holdings (RJH) was comfortable with.
Back to the drawing board and lead architect Marc Woodbury and his team came up with a second design that was remarkably similar to the first, albeit not quite as tall, but the resulting $10-million saving (give or take a million) came at the sacrifice of only three relatively small floor plates of gross floor area.
And this is where the magic happened. As Woodbury points out, an analysis of accounting soon became one of accountability. What would prove to be the best outcome for the environment? Which was the most climate-conscious call? What plan was more sustainable?
Happily, these questions were all relatively easily answerable, given the team at Studio Pacific now had the two corresponding sets of drawings and figures at its fingertips, and the resulting number-crunching became a master’s research paper, which should prove of great interest to the industry.1 Its authors (Emily Howell, Nilesh Bakshi and Marc Woodbury of Victoria University of Wellington and Studio Pacific Architecture) believe this case study is the first of its kind to account for the embodied carbon in a building scheduled for demolition or re-use within the great washup.
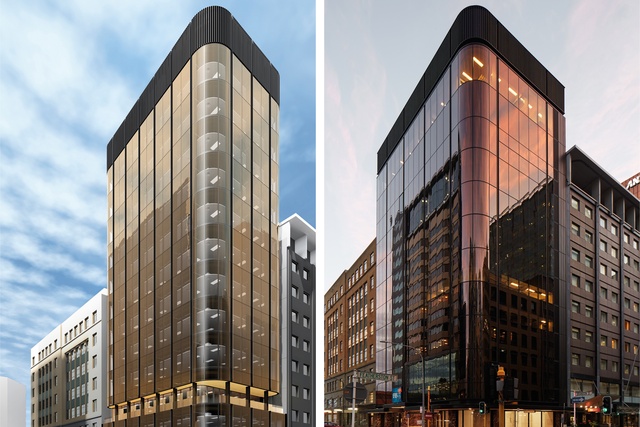
To construct the city’s tallest timber office block would, no doubt, sequester a huge amount of CO2: enough, potentially, to offset half the carbon generated by the necessary concrete core and foundations. But, what of the thousands of tonnes of demolition material created by the removal of its predecessor?
“Designers should consider the carbon they’re responsible for when making design decisions about an existing building,” says Woodbury. “The industry needs to take a holistic accountability approach when considering carbon, which factors in the embodied carbon of the existing materials on site.” This would then be added to the ‘carbon account’ of the new materials required to create another building with a new building design life.
A comparison of the holistic carbon account for each building saw the refurbished project producing a lower carbon density than did the originally proposed low-carbon timber tower. “The cost of increasing the building’s design life by 60 years required about half the embodied carbon of the new build,” said Woodbury.
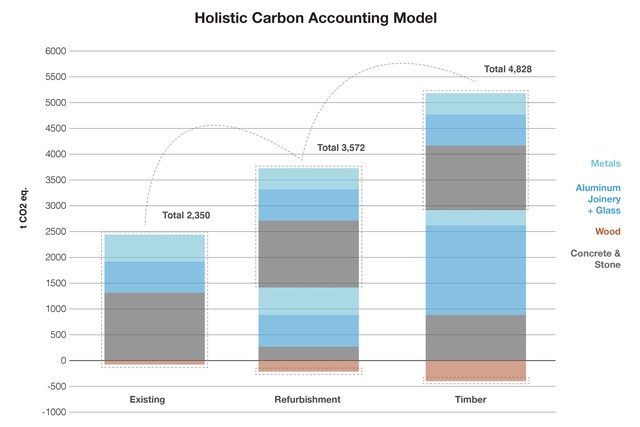
Here’s where the math kicks in. The team’s research had sought to establish the lifetime of a commercial building and determined that 60 years was reasonable. With refurbishment, the total embodied carbon of the existing building is, in part, reused to gain another 60-year life cycle. The original carbon is still contained in the building but only a fraction of it is required to gain another 60 years of life out of it, meaning the carbon footprint for the next six decades is notably smaller. The research indicated that, even when refurbishing with carbon-intensive materials such as glass, aluminium and steel, the lifetime of the existing materials has doubled, lessening the impact. If you take the impact of the existing building and add it to the impact of the new materials required to provide another 60 years, this sum can be divided by 120 years to represent the multiple building cycles.
With Brandon House, refurbishment required an additional 50 per cent of the existing building’s carbon to gain another 60-year lifetime, whereas to build new required an extra 100 per cent. The impact of the new materials in the refurbishment was less than half of that in the new build. Better still, the refurbishment resulted in 10.4t CO2 equivalent (or 25.8 per cent) less embodied carbon over two life cycles when compared to the timber new build. “Accounting for the avoided and added burden [of re-use and demolition] makes the impact dramatically different,” Woodbury points out.
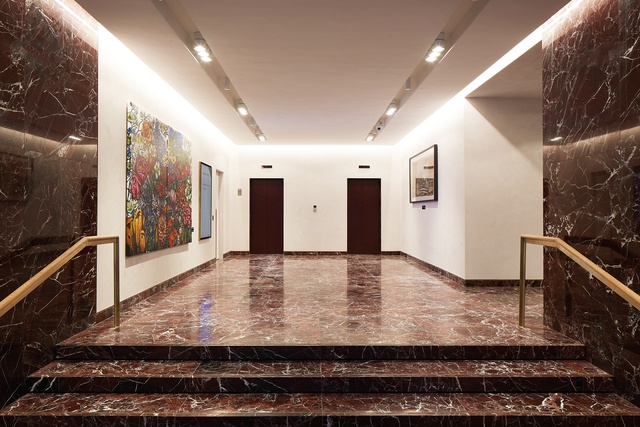
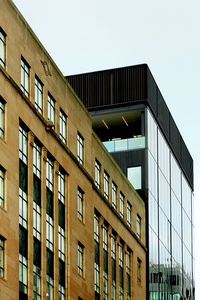
Studio Pacific and the research team also carried out an operational energy analysis and found the refurbishment performed better than the new build would have, by a 16 per cent reduction in CO2 produced over the life of the building. However, Woodbury cautions: “There continues to be emphasis placed on operational energy but this area has greatly improved, with technological advances, passive design and stricter regulations, so, as energy consumption decreases, the significance of embodied energy increases.” Current predictions are that, as the industry continues to reduce emissions associated with operational energy and as the electricity grid decarbonises, embodied carbon will be responsible for 85 per cent of building emissions by 2050.2
To maintain the bulk of the previous building’s structure, strengthen it with FRP (fibre-reinforced plastic) wrapping around the columns, add the curve to the corner, remove the asbestos and re-clad head to toe with double-glazed, heat-reflective glass was just the start. Studio Pacific also added three additional storeys in timber, enabled by the increased structural strengthening to seismic standards, upgraded the services on every floor, created end-of-trip facilities at ground level and reconfigured the lobby area to give the main entrance greater street presence and provide for a retail/hospo tenancy to activate the street corner. Other sustainable initiatives included more than 2400m2 of certified carbon-neutral carpet tile, environmental choice and non-VOC materials, bike parks, electric car charging and metering to allow for a NABERSNZ rating.
The building has, quite rightly, attracted all sorts of awards, not only for its sustainable response to re-use but, also, for its design. The sleek, sculptural tower cuts a commanding presence on the street, with vertical aluminium negatives in the curtain wall helping to break the planar surface and accentuate its height. Dark aluminium fins at the top of the tower discreetly hide the plant floor. While Brandon House has yet to be fully tenanted, it’s sure to attract the kind of boutique businesses associated with the RJH private office lease offering and, as the late, great Fast Show catchphrase goes, we have to say “Suits you, sir”.
The full research paper from Centre for Building Research entitled Holistic Carbon Accounting: Extending the design life of the existing commercial scale building stock by authors Emily Powell, Nilesh Bakshi and Marc Woodbury can be accessed here.
References:
1 Emily Howell, Nilesh Bakshi and Marc Woodbury, ‘Why 60 – A Holistic Carbon Accounting Model: Extending the design life of our current existing commercial scale building stock’, 2020.
2 J Vickers, S Warmerdam, S Mitchell, N Sullivan, J Chapa, S Qian, and G Gamage. ‘Embodied carbon versus operational carbon’, 2021.
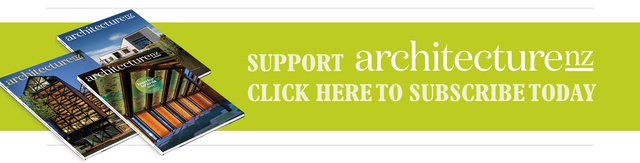